Design to Cost戦略とは何か?事例を交えた概要紹介
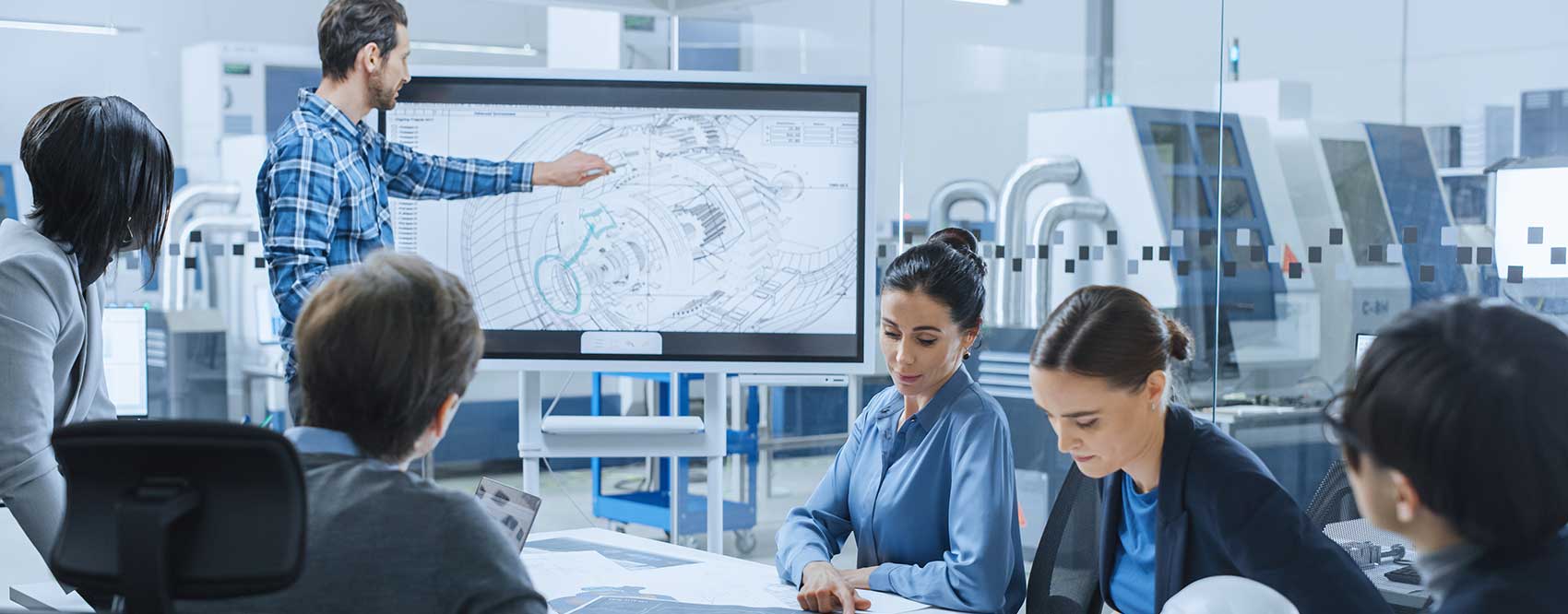
メーカーにとって、コスト削減は常につきまとう目標である。必要な機能を維持しながらコストを下げることは、利益率の向上、市場シェアの拡大、そして顧客満足度の向上を意味します。
しかし、歴史的に見ると、ほとんどのメーカーはコスト見積とコスト管理に、その場限りの戦略に頼らざるを得ませんでした。しかし、もはやそうではありません。
ますます多くのメーカーがコスト管理を合理化するため、製品設計段階のコスト問題になった時に、コスト構造に関する早期の気付きを共有するため、Design to Cost方法論とツールを使用するようになってきています。
Design to Costが、現代の製造業者が理解すべき重要な考え方・価値観である理由はまさにそこにあります。
この記事では、Design to Cost手法を定義し、組織をDesign to Cost手法に移行させるために必要なことを検討し、いくつかの実践例を紹介する。最後に、製造業において、適切なテクノロジー・ツールが、この方法論に不可欠な基盤であることを考察する。
Design to Costとは何か?
Design to Costとは、設計段階における意思決定とコスト管理を統合するための組織的方法論である。
Design to Costの特徴
もちろん、メーカーはこれまでもコストについて考えなければなりませんでした。しかし、従来は、コストは一般的に設計段階の後に行われていました。設計エンジニアが設計を確定する際、性能、外観、信頼性を重視し、全てコストよりも優先されていました。
完成した設計が市場に対してコストが高すぎることが判明した場合、エンジニアは新たなコスト目標に合わせて設計し直さなければなりません。このようなコスト目標は、設計の見通しからは事実上恣意的であることが多くありました。例えば、多くの場合、コスト削減目標は、単に市場価格から望ましい利益率を引くことによって計算されています。
設計のあらゆる側面でコスト削減目標を設定する一方で、最も顕著で、きめ細やかなコストドライバー分析を無視することは、悪い結果を招く要因です。設計エンジニアは、コストに影響の少ない要因を追い求め、設計の機能性を不当に損なう危険性があります。また、最も非効率的なコスト削減要因を特定できなければ、設計は市場の競争力からかけ離れたままになってしまうかもしれません。
ほとんどのメーカーは、製品コストを見積もるために、ある種の厳密な方法を採用している。これは、類似した過去のプロジェクトの引用から、エクセルのスプレッドシートを使った材料費と人件費の合計まで、さまざまなものがある。しかし、製造コストの見積もりは、実際には非常に複雑な分析問題であり、このような簡単に計算ができる原価計算システムは、製品の最終コストとして曖昧な見積もりしか生成しない可能性があります。
インパクトのあるDesign to Cost戦略は、見積もり精度を大幅に向上させる必要があるが、このアプローチは、より正確なコスト目標を追求するだけではない。それは、シミュレーション主導でコスト分析を設計段階に統合することである。その目的は、コスト削減の責任を恣意的な目標からシフトさせることである。その代わりに、Design to Cost環境では、コストは設計上の意思決定に直接結び付けられます。
成熟した "Design to Cost "戦略は、コストを、設計プロセスにただ上乗せされたその場限りのビジネス目標から、設計プロセス内の独立変数へと変える。
製造コスト削減に不可欠な考え方・価値観
製造業における競争圧力は、国際的なサプライチェーンの複雑化と相まって、
ますます多くの製造企業が最新のDesign to Cost戦略に投資するよう促されています。
設計エンジニアは製品の最終コストの70%に影響を与えることができるため、
この戦略は非常に効果的である可能性を秘めている。
設計コストドライバーの全般的な分析を行うには、設計エンジニアは、
潜在的なコストドライバーの膨大な範囲を正確に評価するツールが必要です。考慮する必要がある懸念事項を簡単に列挙すると、以下のようなものがある
材料仕様
直接的なコストに加え、追加的な材料の使用は、間接的に工程コスト、 エコロジーコスト、および以下の他の各要因に影響を与える。公差から加工要件まで、すべてを分析する必要がある。
梱包、配送、ロジスティクス
重量、体積、壊れやすさ、保管要件はすべて、設計の真のコストを評価する上で重要である。
製造可能性
冷却時間から設備の稼働率、設備コストに至るまで、製造可能性は設計のあらゆる面で重要である。
労働力
例えば、手作業での組み立てが必要な部品を追加すると、直接材料費とはかけ離れたコストインパクトが発生する可能性がある。
これらの要素を単独で分析することはできません。すべての設計上の選択は、 設計の他の部分のコストや機能性に影響を及ぼすからです。これらの関係は、重量が増加すれば部品の公差が大きくなるといった明確なものである場合もありますが、(特に設備やサプライチェーンのコストを含めると)非常に複雑な相互作用を示す場合もあります。 このような複雑で、相互に関連し合う変数を考慮するためには、コスト管理を製品エンジニアリングの文化の一部にするという組織の真剣な取り組みと、 製造コスト見積りのための革新的なツールへの投資が必要である。
Design to Cost文化への移行
Design to Costアプローチの背後にあるのは、組織のオーナーシップの問題です。伝統的な設計環境では、コスト管理と価格設定を管理する事業部門(営業またはビジネス開発や、多くの場合は上層部からの密接なインプット)と実際の設計チームとの間に大きな断絶が存在する可能性があります。よく言えば、全体的なコストドライバー評価実施を妨げる組織の縦割りを引き起こす程度です。悪く言うと、コスト目標の実現可能性をめぐって、エンジニアリング部門と他の事業部門との間で縄張り争いが起こることもある。 コスト管理、機能設計、顧客ニーズ/市場価格に関する組織の考え方を一致させるためには、効果的な原価計算戦略によって、設計エンジニアにコスト管理を統合する責任、権限、ツールを与えなければなりません。
このシフトには確かにエンジニアリング文化の変革が必要ですが、コストマネジメントを設計段階に導入することは、単に新しい専門用語を覚えるだけの問題ではありません。多くの重要なコストドライバーは現場レベルの製品エンジニアにとって不透明なものです。エンジニアは、専門家のリソースに負担をかけたり、イノベーションを妨げたりすることなく、設計段階でコストを総合的に分析するのに役立つツールを必要としています。
例えば、設計の代替案を検討しているエンジニアは、特定の部品を追加することにおいて、わずかな材料費を追加するだけで、信頼性を向上させながら設計が済むと考えるかもしれません。しかし、それぞれのごくわずかな追加は、最終的なコストに単純に影響を与えるわけではありません。いくつかの部品が追加された後、全体の設計は重量のしきい値を超え、レンタル料の高い第二の設備で製造する必要があります。さらに、この2つ目の施設は、関税が高く、為替レートの差が1つ目の施設より不利な国にある。設計上の決定が及ぼす複雑な影響は、従来の設計者が合理的に予想できるよりもはるかにコストがかかる可能性がある。
以前は、これらの要素を、設計代替案を比較する際に定量化することはほとんど不可能でした。 しかし今日、適切なテクノロジー・ツールがあれば、この問題は解決可能です。
適切な原価計算システムは、Design to Costを実現するために不可欠である
aPrioriのようなインパクトのある製造コスト見積もりソフトウェアは、設計のコスト構造のあらゆる要素に活発な分析を提供する方法論として、重要な基盤として機能します。そのためにaPrioriは、人件費や原材料から非常に特殊な製造工程まで、すべてを含む高度な原価計算モデルを必要とします。 実際、aPrioriは3D CADファイルと直接連携し、設計にとって非常に重要な環境ででコストドライバーを分析します。
強固な原価計算戦略には、製品のコストドライバーの計算だけでなく、代替設計のコストドライバーの分析をビジネスのスピードで生成する能力が必要であるため、このような技術力は不可欠である。
例えば、Spirit Aerosystems社(航空宇宙部品メーカー)は、ある部品がコスト目標を超えていることに気づきました。 aPrioriは、経験の浅い設計者が、一見わずかな美観の選択をしたことがすぐに判明し、実際、その部品全体のコストを10%以上押し上げていることがわかりました。 SpiritがaPrioriを使って、どのように余計な設計上の特徴を特定し、排除したかは、ビデオでご覧いただけます。
本記事はaPriori社からの転載記事です。オリジナルのサイトで記事を読む。
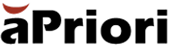
組織を横断したコスト領域のDX
aPrioriは、3Dモデルから製造原価算出を可能にするデジタルファクトリーの構築を提供し、組織を横断したコスト領域のDXに貢献します。