ADVENTURECluster Overview
Overwhelming calculation speed
Calculate a model that you had given up on due to scale with full assembly
ADVENTURECluster is a domestic large-scale structural analysis software developed by Allied Engineering Corporation (SCSK Gr.). It is capable of computing large-scale analysis models with tens to hundreds of millions of degrees of freedom at overwhelming speed. Its scalability and high speed can wipe out problems in large-scale analysis that were previously given up on, and dramatically increase the potential of CAE. In addition, because it frees users from geometry data simplification and advanced mesh modeling techniques, it is also being used by "newcomers" who are handling CAE for the first time and "designers" whose main job is not CAE. The number of users has been increasing year by year. The analysis functions are expanding year by year to meet the needs of a wide range of customers.
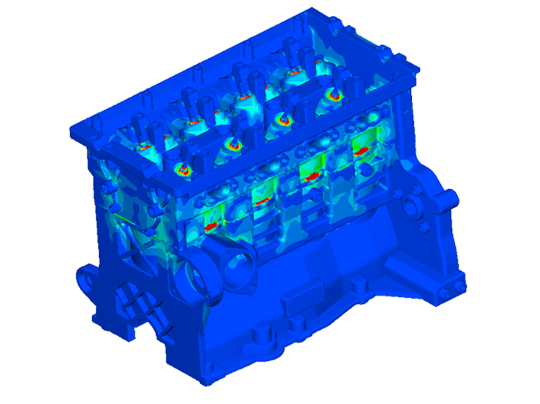