デジタルツインとは?ソフトウェア動向を踏まえたCAE戦略的活用と実現への道筋
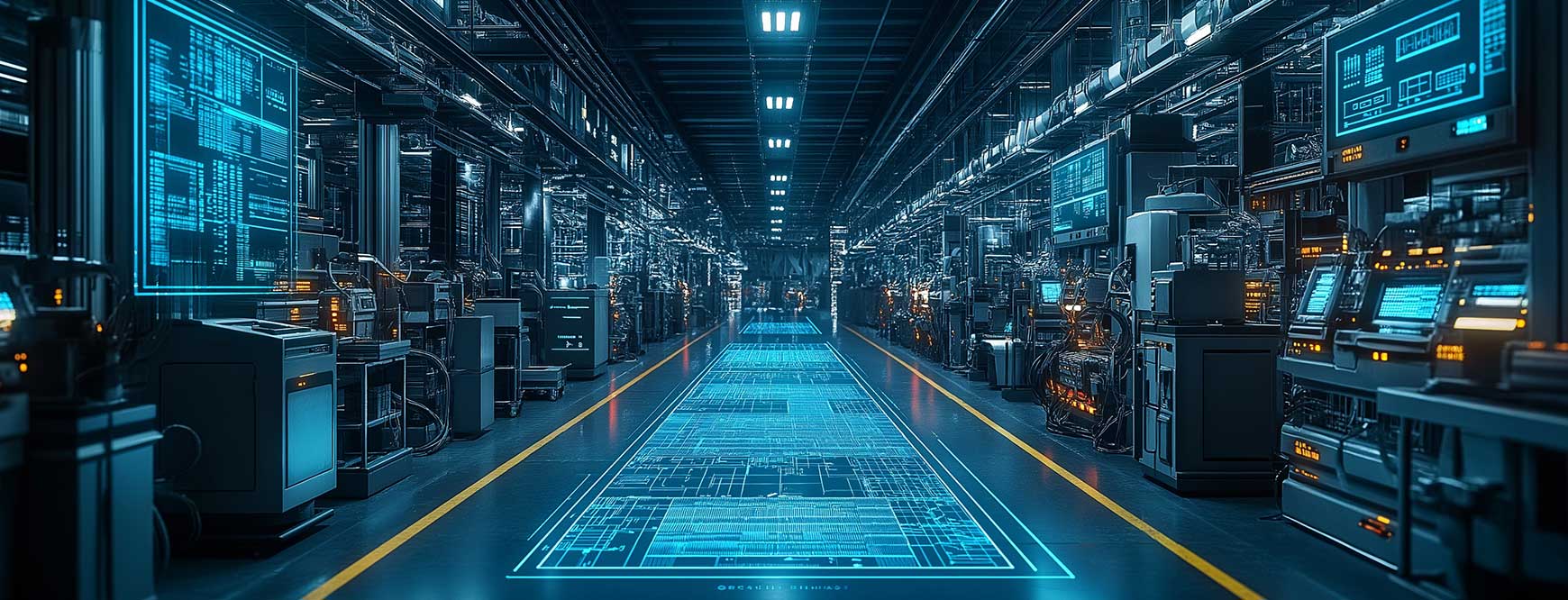
製造業におけるデジタル技術の活用は、成長戦略の重要なアプローチの一つです。この取り組みの中核を成すのが「デジタルツイン」であり、物理的な製品、設備、プロセスをデジタル空間で再現することにより、検証の並列化と多数のトライアンドエラーをフィジカル空間の制約なしで実施できます。これにより膨大な試行を高速かつ柔軟に取り組むことができるため、新たな価値と革新的な業務プロセスの創出が可能になります。これは、製造業において重要なデジタルトランスフォーメーション(DX)戦略として注目されています。
本稿では、製造業におけるデジタルツインの実現に向けたCAEの活用を、データの生成、活用、およびモデルの展開の三つの観点から検討し、それぞれに必要な技術要素について解説します。まず、デジタルツインの定義を確認し、次にCAEの基本と動向を概観します。その後、データの生成と活用の観点からCAEにAIを適用する方法を検討し、展開の観点から得られた知見をどのように組織横断的に広げるかを考察します。最後に、デジタルツイン実現の道筋について技術的要件と非技術的要件の観点からまとめます。
1. デジタルツインとは
「デジタルツイン」とは、物理的な製品、設備、プロセスをデジタル空間で精密に再現した仮想モデルです(1)。デジタルツインの概念は、2002年にミシガン大学のマイケル・グリーブスによって提唱され、2010年にNASAによって更に発展し、実用的な定義がされました。デジタルツインは、フィジカル空間とデジタル空間、そして両者の連携の3つの要素から構成されます。フィジカル世界の現象や物体をデジタルデータで表現し、そのデータを用いてシミュレーション、分析、予測を行うことを可能にします。これにより、製品の設計から運用、メンテナンスに至るまでのライフサイクル全体を通じて、リアルタイムのデータと連動し、新たな知見や気づきを素早く提供します。
製造業におけるDXにおいて、デジタルツインは製品開発の効率化、品質向上、市場適応の迅速化を実現する重要な要素です。デジタルツインを活用することで、製品の設計段階での問題点の特定、運用中のパフォーマンスの最適化、未来の故障予測などが可能になり、企業の競争力を大きく高めます。
デジタルツインの応用は多岐にわたります。例えば、自動車産業では、車両や街のデジタルツインを活用して、安全性の向上や新しい機能の迅速な開発が行われています(2)。また、スマートファクトリーでは、製造プロセス全体のデジタルツインを構築し、AIを活用した工程設計や効率的な生産管理・品質管理の実現が検証されています(3)。
デジタルツインの技術は進化し続けており、IoT、CAE、AI、通信技術などのデジタル技術の統合により、高度な応用が期待されています。デジタルツインの仮想モデルで様々な検証を高速に実施することで、企業はより柔軟かつ迅速に市場の変化に対応し、社会変化に対してレジリエンスの高い持続可能な製品開発と運用体制の構築が可能になると考えられています。
2. デジタルツインとメタバースの違い
デジタルツインとメタバースは、どちらも仮想空間やデジタル技術を活用していますが、実世界の物理的なオブジェクトとの関わり方に違いがあります。
デジタルツインは、物理的なオブジェクトやシステムのデジタルコピーを作成し、これを用いてリアルタイムでの監視やシミュレーションを行います。その主な目的は、現場での効率的な運用や意思決定をサポートすることです。具体的には、工場の設備や車両、建物などの運用状況を監視し、問題の早期発見や最適化を目指します。仮想空間と現実世界の双方を視野に入れて現場の活動を支援する方法論と言えます。適用される工程としては、製造・保守運用などの下流での使用ケースが多いです。
一方、メタバースは、目的に応じて構築された仮想世界です。エンターテインメント領域では、ユーザー間の交流や経済活動を支援する仕組みを提供する例があります。近年では、各産業の特性を考慮して構築されたインダストリアルメタバースが注目されています。製造業では、シミュレーションやAIで予測・分析した結果を共通の仮想空間で再現することを目指しています。ただし、物理的な現実世界との連動が必ずしも求められるわけではない点がデジタルツインと異なります。適用される工程としては、企画や設計などの上流での活用が検討されることが多いです。
このように、デジタルツインは主に現実世界と連携して精密な再現と最適化を目指す技術アプローチであり、メタバースはその目的に応じた内容で構築された仮想空間です。
3. デジタルツインとシミュレーションの違い
デジタルツインは物理的なものに対してリアルタイムな応答と反映を繰り返すのに対し、シミュレーションは時間がある程度かかっても未来の状態や仮定の動作を再現するという挙動の違いがあります。デジタルツインは、現実のデータや設備を使用してシステムの挙動を観察・最適化し、シミュレーションは仮定された条件での動作やシナリオをテストすることに主眼を置いています。
デジタルツインは、センサーやデータ収集技術を使って、対象の状態や動作を正確に反映させ、運用中の実データを仮想空間で観察・分析します。これにより、現実世界の状態を仮想的に把握し、予測や最適化を行うことが可能になります。デジタルツインはリアルタイムで進行中の情報を反映させることが特徴です。デジタルツインでシミュレーションやAIを活用する場合、リアルタイムな応答が要求されます。
シミュレーションは、特定の条件やパラメータに基づいて仮想的にシナリオを再現する手法です。シミュレーションは通常、モデルに基づいて仮定を立て、その結果を予測することを目的としています。シミュレーションは実際のデータを必ずしもリアルタイムで取り入れませんが、未来の動作を予測するために使用されます。また、予測にかかる時間もリアルタイム性は求められておらず、一定の計算時間を要することがほとんどです。
このようにデジタルツインはシミュレーションを内包することがありますが、通常のシミュレーションの活用と異なり、リアルタイムな応答を実装する必要があります。
4. デジタルツインのメリット
製造業におけるデジタルツインの効果は、製品開発の効率化、品質の向上、市場への迅速な適応の3つが主に挙げられます。これは、IoT、CAE(コンピュータ支援工学)、および関連ソフトウェアの進化と適用によって支えられています。
CAEの活用
デジタルツインの実現には、特にCAEの活用が不可欠です。 モデリングおよび計算機器の高度化により、デジタル空間におけるフィジカル情報の正確な再現・予測可能な領域が拡大しています。これにより、フィジカル空間で視認できる現象の再現はもちろん、IoTなどを介して取得したフィジカル空間の情報だけでは把握しきれない製品や設備に関する情報を可視化することができます。
品質の向上
製品開発から製造、保守に至るまでのすべてのデータを一元化し、品質管理を強化することで、品質向上に向けた効率的かつ透明性のある管理を実現します。リアルタイムでの品質監視により、問題を早期に発見し、迅速に対応することが可能になります。また、製品のトレーサビリティが向上することで、品質問題が発生した際にはその原因を遡って特定でき、効果的な改善策を講じることができます。これにより、製品の品質を一貫して維持し、最終的には顧客満足度の向上にもつながります。
市場への迅速な適応
デジタルツインを利用すると、製品のデジタルコピーを通じてリアルタイムで市場の変化を把握できます。これにより、消費者の反応や競合の動きを即座に認識し、素早く戦略を変更できます。製品のデザインや機能をシミュレーションでテストし、実際の市場ニーズに合わせて調整することが可能です。また、過去のデータを基に需要の変動を予測し、生産計画を柔軟に調整できます。これにより、新製品の市場投入をスピードアップし、競争優位性を確保できます。
5. デジタルツインのデメリット
デジタルツインの実現において、CAEの計算時間の長さとデータや設定した物理モデルの管理・統合は課題となっています。以下に、デジタルツインの主なデメリットをあげます。
計算時間の長さ
デジタルツインの実現において、CAEの計算時間が長いことが大きな課題となります。通常、計算には数時間以上かかることが多く、設計リードタイムを短縮するためには、より効率的な計算方法が求められます。これにより、迅速な意思決定をサポートするための計算速度の向上が必要です。
データとモデルの管理・統合
デジタルツインでは、フィジカル空間とデジタル空間を融合させるため、膨大なデータと複雑な物理モデルの管理・統合が求められます。これらのデータは急増し、効率的に運用するためには、精密なデータ連携と管理体制が不可欠です。意思決定のスピードを加速させるためには、各領域でのCAE分析結果を前倒しで連携し、活用する必要があります。
複雑なデータ処理とリソース負担
デジタルツインを運用するには、高度なインフラと大規模な計算リソースが必要です。複雑な物理現象のシミュレーションや大量のデータ処理には、計算能力やストレージのコストがかかります。また、リアルタイムでデータを処理・更新することが求められるため、これらのリソース負担が大きくなる可能性があります。
データの整合性と互換性
データとモデルの整合性を保ちながら、異なるシステム間でのデータ互換性を確保することは大きな課題です。複数のシステムやプラットフォーム間でデータを連携させる際、情報の不一致や更新の遅れが発生することがあります。これにより、全体の運用が効率的に行えなくなる恐れがあります。
6. 製造業でデジタルツインが注目される背景
近年、製造業はデジタル化の進展とともに、効率性の向上や生産性の改善を目指す動きが強まっています。その中で、デジタルツインはリアルタイムで物理的な資産やプロセスを仮想的に再現する技術として、大きな注目を集めています。 デジタルツインが製造業においてどのように活用され、具体的にどのような効果をもたらしているのかを詳しくご説明いたします。
1. 効率化とコスト削減のニーズ
製造業では、コスト削減や生産性向上が常に求められています。デジタルツインを活用することで、製品や設備の状態をリアルタイムで監視・分析することができ、故障や問題の予兆を早期に発見することが可能になります。これにより、メンテナンスの最適化やダウンタイムの削減が実現し、全体的な運用コストの削減に貢献します。
2. データ活用の進化
製造業では、IoT(モノのインターネット)技術を用いて、各種機器や設備から膨大なデータが収集されるようになりました。このデータを効果的に活用するために、デジタルツインが登場しました。リアルタイムのデータをもとに仮想モデルを構築し、シミュレーションや予測を行うことで、意思決定が加速します。これにより、製品開発や生産工程においてより精密な調整が可能となり、市場の変化にも柔軟に対応できるようになります。
3. 競争力の強化
製造業は競争が激しく、迅速な製品投入や市場のニーズに応じた柔軟な対応が求められています。デジタルツインは、設計や生産プロセスの効率化だけでなく、新製品の開発期間の短縮にも寄与します。仮想空間でのテストやシミュレーションを通じて、製品の改善案やリスクを事前に把握することができ、最適な製品を迅速に市場に投入するための強力なツールとなります。
4. 持続可能性と品質の向上
近年では、環境への配慮や品質管理が製造業における重要なテーマとなっています。デジタルツインを活用することで、製造工程の無駄を減らし、エネルギー消費や資源の最適化が可能となります。また、製品の品質を向上させるためのデータ分析が進み、品質管理がより精密かつ効率的になります。このような取り組みは、環境負荷の軽減や持続可能な製造を実現するために大きな役割を果たします。
5. 未来の製造業への対応
製造業はますます高度な技術と結びついて進化しています。自動化やAI(人工知能)との連携が進む中、デジタルツインはその基盤となる重要な技術として位置付けられています。製造業の将来に向けて、デジタルツインを導入することで、さらに複雑化する製造プロセスに対しても、効率的かつ予測的な対応が可能となります。 このように、デジタルツインは製造業において、コスト削減、効率化、品質向上、そして持続可能性に向けた大きな一歩を踏み出すための重要なツールとなり、業界全体で注目を集めています。
7. CAEの進化とAI技術の活用
CAEは、製品の設計、分析、製造プロセスをデジタルで支援する技術です。CAEは、コンピュータの進化とともに、複雑なシミュレーションや解析が可能になりました。初期のCAEツールは主に構造解析や熱流体解析に限られましたが、今では電磁気学、材料科学、生産工程に特化したものなど、より広範な分野にその応用が拡大しています。
CAEの進化は、機器の計算能力の成長、アルゴリズムの改善、ユーザーインターフェースの向上によって推進されてきました。特に、高性能コンピューティング(HPC)の発展は、より複雑なシミュレーションを短時間で実行することを可能にしました。また、クラウドコンピューティングの普及により、高度なCAEツールをより多くの人が手軽に使用できる環境が整ってきています(4)。
デジタルツインの概念の普及に伴い、CAEはデジタルツインの重要な構成要素となっています。CAEを通じて得られる詳細な結果は、デジタルツインの精度を高めています。実際、製品内部の時系列変化や設備内の挙動などフィジカル空間のみでは得られない情報を取得することができます。
一方、CAEの課題として計算時間の長期化とデータ・モデルの管理・統合が挙げられます。計算時間について、デジタル技術の発展に伴い、従来よりも速く計算できるようになっていますが、一回の計算に数時間から数日を要します。したがって、デジタルツインが要求するリアルタイム性をCAE単体で満たすことは困難です。
また、データ・モデルの管理・統合について、CAEは操作やファイル構造の複雑性から組織をまたいだ連携を難しくしています。例えば、あるユーザーが作成した解析モデルをそのまま保存していても、情報がCAEのソフトウェアに閉じられ外部から確認する場合は都度CAEソフトを立ち上げる必要があります。また環境の差異によりある端末で実行できたことが別の端末では実行できないといったトラブルがよく発生します。
またAIで構築したサロゲートモデルを簡易なファイルに変換し展開することで、CAEのデータのままよりも柔軟な展開ができます。例えば、CAEのデータで展開した場合、CADモデル情報や解析情報を含むためデータ保存容量の問題はもちろん、製品詳細情報の流出の懸念があります。一方、サロゲートモデルの場合、モデル情報や材料情報などを含めずに展開できるため、軽量かつ機密性高く取り扱いができます。サロゲートモデルのファイルは汎用的なものが多く、あらゆるアプリケーション、システムに組み込むことができます。これにより、習熟したユーザーにはCAEのデータそのものを、普段使い慣れていないユーザーや結果のみを展開するだけでよい場面ではサロゲートモデルを展開するなど柔軟な展開が実現できます。
8.デジタルツイン実現のためのCAE活用
デジタルツインにCAEの効果を活用するためには、AI技術の適用が必須です。本章ではAI技術を適用するために必要な要素である、データの“生成”・“活用”・モデルの“展開”についてCAE活用を念頭に解説します。
8.1.データの生成
製造業におけるデジタルツイン実現にCAEを適用する場合、効率的なデータ生成は不可欠です。したがって、証明したい仮説に対するデータを必要最低限な回数で取得する必要があります。このような場面において、実験計画法(DoE)はデータ生成のプロセスの中心的な役割を果たします。ここでは、具体的な関数を例にDoEの効果を説明します。
(1)DoEの適用
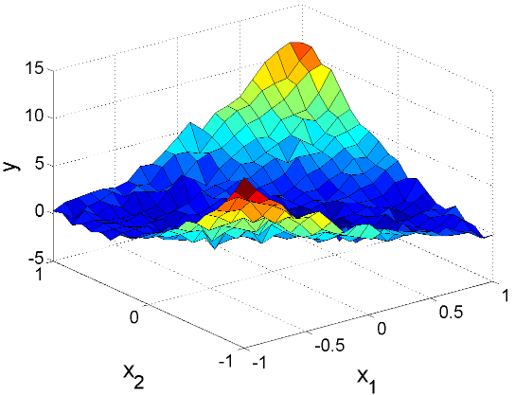
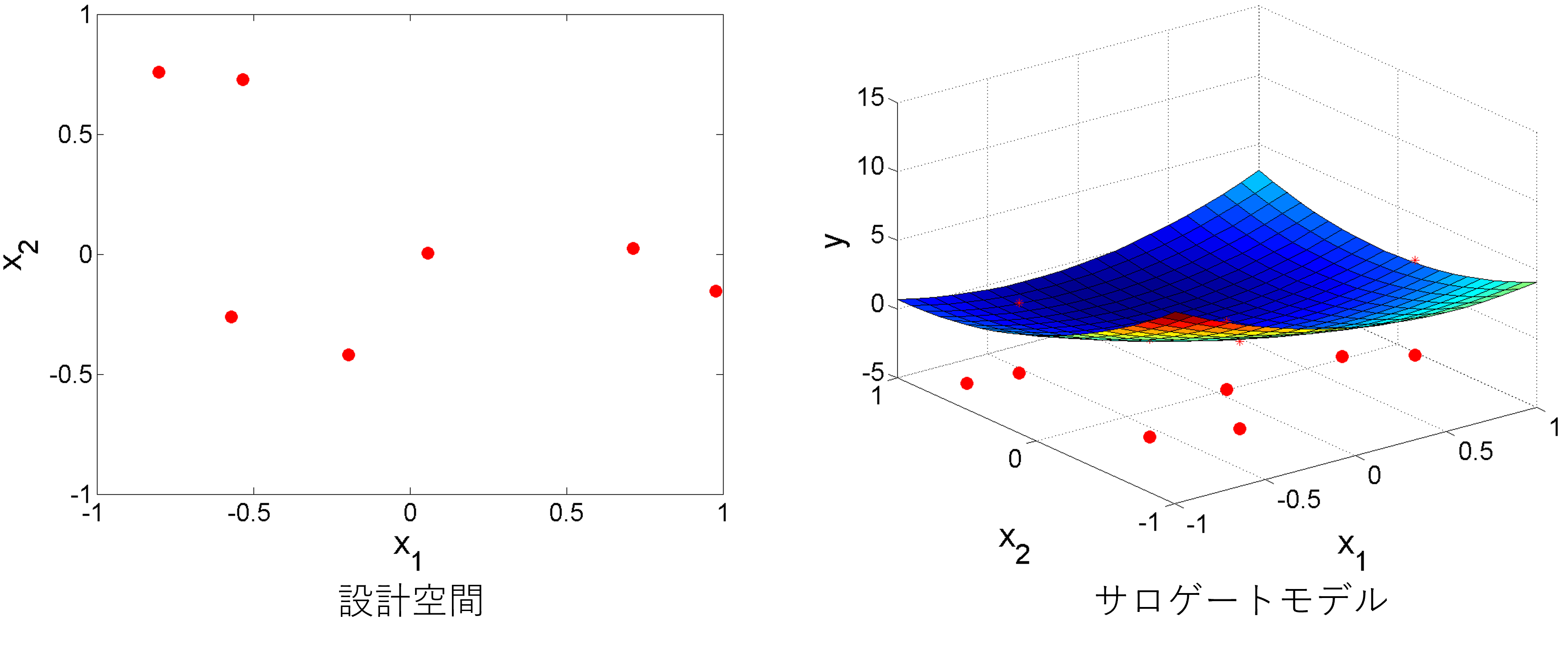
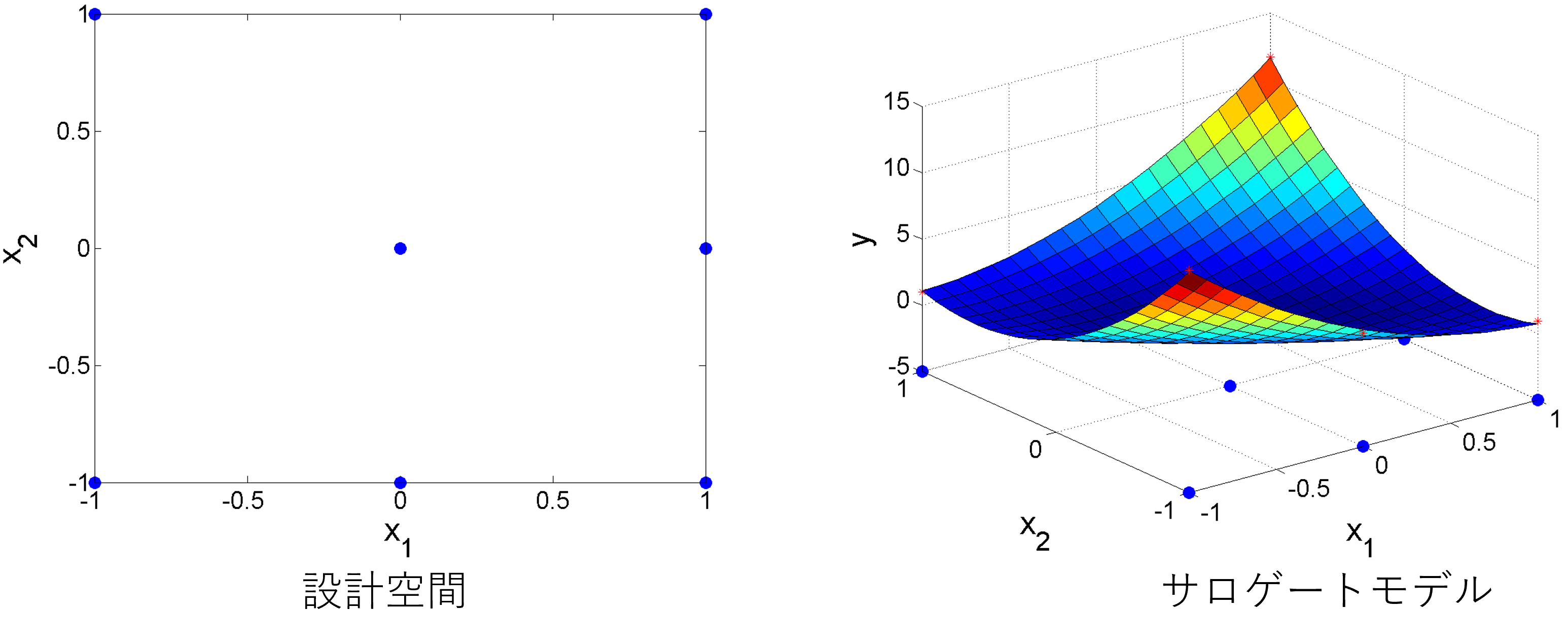
この比較は、AIの適用においてデータの質は予測精度に寄与する重要な要素であることを示唆します。AIは学習した範囲内であれば予測精度が高くなりますが、範囲外であれば予測は難しくなります。また学習範囲内であっても、偏りがあれば予測が難しくなります。実際、先程のランダムの場合のグラフをみると、取得した点付近は予測精度が比較的高く、点から離れた領域は予測精度が低いことがわかります。したがって、高度なデータ活用には効率的なデータ生成が重要です。仮にサンプルサイズが大きくても、偏りがあるなどデータの質に課題があればAIの精度は低くなる可能性があります。事前にデータを可視化し、データの特性を把握した上で、追加のデータ取得が必要なのかあるいは十分なのかなど判断を行うことが求められます。
8.2.データの活用
データ活用は、製品開発とプロセス最適化を支援し、設計リードタイム短縮に大きく寄与します。サロゲートモデルは製品の性能を高速にシミュレートすることができるため、計算時間のボトルネックを解消できるからです。例えば、サロゲートモデルを活用せず複数の現象を考慮した最適設計を導出したい場合、複数のCAEを連携し解析する必要があります。これはCAEの計算時間が積み重なり、一回の計算時間が長期化する懸念があります。そのため、十分な検討ができず、設計に含めたい要素を後工程にまわしてしまうことがあります。一方、サロゲートモデルを用いた場合、該当箇所の現象の予測は数秒以内に終わるため、計算時間を短縮しつつ、考慮したい現象を設計に反映することができます。
本節ではサロゲートモデルの構築手法として「テーブルデータを活用した機械学習手法」と「3Dモデルファイルを活用した機械学習手法」の2種類を取り上げ、それぞれの特徴とメリット・デメリットを整理します。
(1)テーブルデータを活用した機械学習手法
この手法では、テーブル形式のデータを用いて、サロゲートモデルを構築します。テーブルデータには温度、圧力、材料特性などのパラメータがよく記載されます。また、形状の寸法レベルの情報を含めることで形状情報を予測に利用することも可能です。 メリットとしては解釈性の高さと小さなサンプルサイズから始められることの二つが挙げられます。解釈性の高さについて、テーブルデータを対象とした機械学習手法ではシンプルなモデルになる場合があります。入力と出力の関係が可視化されやすく、なぜそのような予測をしたのかユーザーが考察しやすいです。昨今では関係が可視化しにくいAIであっても可視化できるSHAPなどの手法を活用した説明可能なAI(XAI)の取り組みが増えています(8)。ただ、あくまでもこれらは構築したサロゲートモデルの関係を示しているのみで、現象の因果関係を示しているわけではありません。したがって、因果関係を確認する場面では状況に応じて別の方法を検討する必要があることに留意したいです。サンプルサイズについて、設計に関するサロゲートモデル構築において、テーブルデータで取り扱う変数の数は小規模、具体的には変数が50種類以下である場合が多いため、比較的小さなサンプルサイズから始められます。CAEや実機からデータを取得する場合、いずれも時間とコストがかかり容易にサイズを大きくできない。可視化ツールや統計処理などを使用し、データの関係から不要な変数を間引くなどして小さなサンプルサイズで対応できるよう前処理を検討することが重要です。
本手法のデメリットとして、データの質の依存度が高いことが挙げられます。小さなサンプルサイズで学習ができますが、各データの内容がサロゲートモデルに反映されやすいです。つまり、誤ったデータや学習に適さないデータが少しでもあると予測精度の向上を難しくします。目的に対してデータの内容に不備がないかなど現場の知見を含めた総合的な判断が必要です。
(2)3Dモデルファイルを活用した機械学習手法
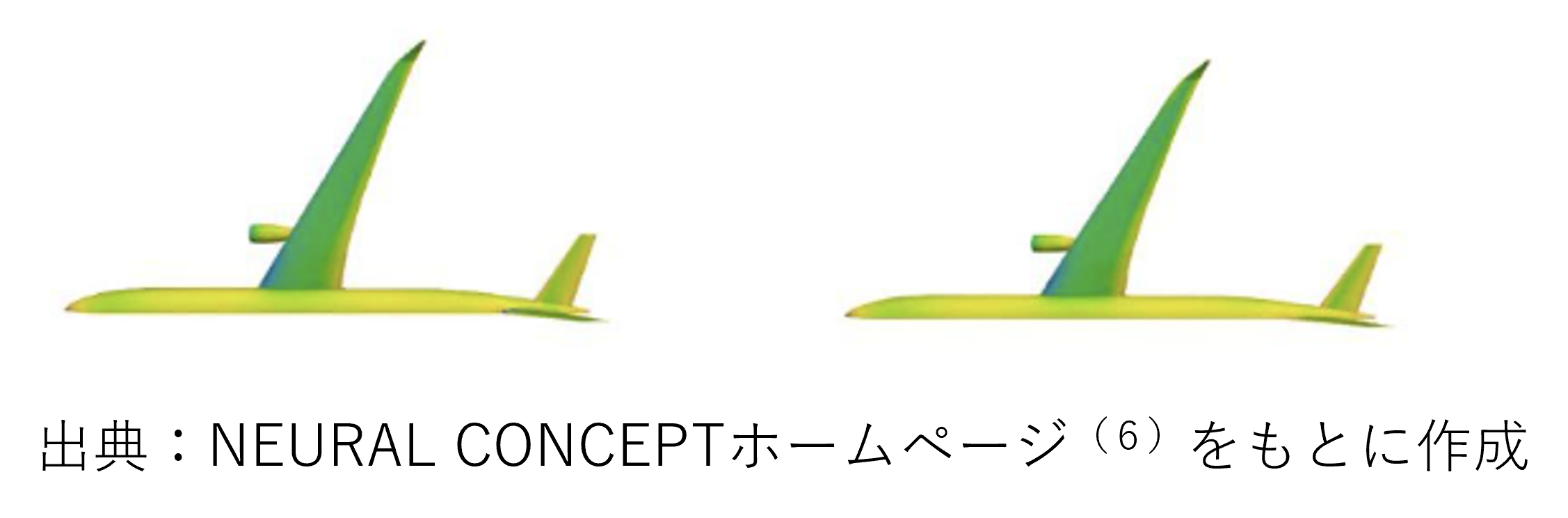
デメリットとして、この手法ではモデルデータを利用しているため、必要なサンプルサイズが大きくなります。誤解を恐れず説明すると、一つ一つのメッシュ・節点情報を変数とみなして学習するため、入力変数の数が膨大になります。最近では商用のソフトウェアとして3Dモデルを取り扱うサロゲートモデル構築ソフトが増えています(6)。多くの場合、提供ベンダーの工夫によりユーザーが用意する必要なサンプルサイズを比較的小規模に抑えながら、高精度なモデル構築ができます。
ただし、AIに使用するデータとして形状情報を含めるため、値の範囲や網羅性の確認がテーブルデータよりも難しいです。したがって、実際に業務に活用する場合は、「データの生成」のプロセスで、データの増やし方や内容を十分に調査・検討することが重要です。
8.3.モデルの展開
製造業におけるデジタルツインの実現に向けたCAEの戦略的活用では、データの生成と活用に続き、その「展開」が重要な役割を果たします。特に、AIを使用して構築されたサロゲートモデルの組織横断的な活用は、製品開発プロセスの効率化と最適化に不可欠です。
サロゲートモデルを組織全体で共有し活用することで、異なる部門が同じ基盤の上で意思決定を行い、製品設計から生産、メンテナンスに至るまでの一貫した最適化が可能になります。特に以下の3つのメリットがあります。
・知識の共有と再利用:サロゲートモデルを通じて、特定の専門知識や解析結果を組織内の異なる部門で共有することができます。これにより、知識の再利用が促進され、設計や解析の効率が向上します。
・意思決定の迅速化:サロゲートモデルを活用することで、複雑なシミュレーション結果を迅速に取得できます。これにより、設計変更の影響を素早く評価し、迅速な意思決定が可能になります。
・組織横断的な最適化:異なる部門が同じサロゲートモデルを使用することで、製品の設計から製造、運用に至るまでのプロセス全体を通じた最適化が実現できます。これにより、製品の品質向上とコスト削減が可能になります。
・アクセスと共有の管理:組織内でモデルを共有する際には、適切なアクセス権の管理が必要になります。ある組織には閲覧許可を与えますが、他は拒否するなど組織ルールやプロジェクトの要件に応じて柔軟に変更することが求められます。
・モデルの更新と管理:構築したサロゲートモデルやプロセスは、新しい知見が得られるたびに更新し、常に最新であることが求められます。モデルのバージョン管理と更新プロセスの標準化が必要です。
・ユーザーのレベルに応じた展開:すべてのユーザーが複雑なCAEやプログラミングを理解し活用することが理想ではありますが、多くの企業で実現は難しいです。図6はある企業がヒアリングを元に作成した製造業におけるデジタルスキルレベル別の人数比の一例です(10)。図6をもとに考えると、ユーザーの多くがデジタルツインを実現するための十分なスキルセットを保有していません。したがって、デジタルツールに慣れていない人や詳細な結果が不要なユーザー向けにはノーコードで簡単に計算が実施できる環境を提供し、別のユーザーには工夫の自由度がある程度供されたローコード環境を提供するといった、目的・レベルに適したツールの展開が必要です。
近年では、このような課題を解決しながらメリットを享受可能な製品が提供され始めています。実際、ある企業ではプロセス自動化とモデル展開プラットフォームを既に導入しており、サロゲートモデルに限らず、DoEや最適化などのプロセスやCAEなどの物理モデルを含めて共通のプラットフォームに集約し、組織全体へユーザーレベルに応じた展開を実現しています。これにより、従来の業務プロセスと比較し3倍の生産性向上を達成しています(11)。つまり、現時点においてCAEをはじめとしてデジタルツインを実現するための技術的要件は満たすことが可能であり、各社の製品やソリューションを導入・連携次第で課題を解決できる状況です。言い換えると、技術的要件のためのインフラやツールが整っている現在、非技術的要件への対応こそが企業が直面している最も重要な課題となっています(12)。これには、組織文化の変革、異なる部門間の連携強化など多くの企業が抱えるジレンマが含まれます。解決には大きな理想を描き、そこに至るために必要な取り組みを細分化し、長期に渡るプロジェクトに対して粘り強く推進することが求められています。
9.まとめ
製造業におけるDX戦略には、デジタルツインが重要であり、CAEの戦略的活用が求められています。データ生成、活用、そしてモデル展開の各フェーズには固有の課題が存在しますが、これらの技術的要件に対する解決策は次第に明らかになりつつあります。しかし、デジタルツインの実現は、企業文化の変革を含む長期的な取り組みを必要とし、長期目線での理想を明確に設定し、それに向けて粘り強く取り組むことができる人材と体制の構築が求められています。本稿で紹介した手法、ツール、そしてデータは、あくまで手段に過ぎません。これらの手段を適切に活用することで、製品開発プロセスの効率化を実現し、社会課題の要求と自社成長の両立を達成できる持続可能な体制を構築するための明確な道筋が描かれます。
1) 三島一孝,MONOist,いまさら聞けない「デジタルツイン」,MONOist,https://monoist.itmedia.co.jp/mn/articles/1808/08/news043.html,(参照 2024.02.19)
2) トヨタ自動車,森田記者が見た「未来の都市」の現在地,トヨタイムズ,https://toyotatimes.jp/report/constract_wovencity/001.html,(参照 2024.02.19)
3) READY ROBOTICS:Toyota Motor Corporation Collaborates with READY Robotics to Introduce Sim-to-Real Robotic Programming in Industrial Manufacturing Using NVIDIA Omniverse,READY ROBOTICS,https://www.ready-robotics.com/press-releases/toyota-motor-corporation-collaborates-with-ready-robotics-to-introduce-sim-to-real-robotic-programming-in-industrial-manufacturing-using-nvidia-omniverse,(参照 2024.02.19)
4) Rescale:クラウド向けに構築されたハイパフォーマンスコンピューティング,Rescale,https://rescale.com/ja/,(参照 2024.02.19)
5) Sascha Ranftlほか, Bayesian Surrogate Analysis and Uncertainty Propagation,The 40th International Workshop on Bayesian Inference and Maximum Entropy Methods in Science and Engineering(2021),https://www.mdpi.com/2673-9984/3/1/6(参照 2024.02.19)
6) NEURAL CONCEPT:3D Deep learning AI for Engineering,NEURAL CONCEPT,https://www.neuralconcept.com/shape,(参照 2024.02.19)
7) pSeven:Generic Tool for Design of Experiments (GT DoE),pSeven, https://www.pseven.io/product/pseven-core/generic-tool-for-design-of-experiments/(参照 2024.02.19)
8) Scott Lundbergほか, A Unified Approach to Interpreting Model Predictions,NIPS’17,4768-4777(2017),https://dl.acm.org/doi/10.5555/3295222.3295230(参照 2024.02.19)
9) Masanobu Horieほか,Physics-Embedded Neural Networks: Graph Neural PDE Solvers with Mixed Boundary Conditions,NeurlPS2022,https://proceedings.neurips.cc/paper_files/paper/2022/file/93476ae409ae3246e22a9d4b931f84ed-Paper-Conference.pdf(参照 2024.02.19)
10) pSeven:BUILD,DEPLOY AND OPERATE DIGITAL TWINS AT SCALE WITH PSEVEN ENTERPRISE,pSeven,https://www.pseven.io/assets/files/media/enterprise/pSeven-enterprise-brochure.pdf(参照 2024.02.19)
11) pSeven:ARENA, the future of engineering for flowline studies,Youtube, https://www.youtube.com/watch?v=qn1mji09704&t=1282s
12) 経済産業省:2023年版ものづくり白書https://www.meti.go.jp/report/whitepaper/mono/2023/pdf/honbun_1_5_2.pdf,(参照 2024.02.19)
「自動車技術」Vol78 No6 類似記事掲載
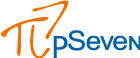
最適化/機械学習による設計空間探索ソフトウエア pSeven Desktop
pSeven Desktopであらゆる設計リードタイムを短縮。煩わしい作業を削減し、CAD・CAE・データとプロセスを自動化します。pSeven Desktop独自のAIと強力な自動化エンジンによって、最適な設計条件を効率的に発見が可能です。