開発者に聞く ~ クルマの設計開発において増大するワイヤーハーネス・ホースの課題とその解決方法とは
- 解析シミュレーション
- インタビュー
- モノづくり
- ../../../article/2021/01/ips2.html
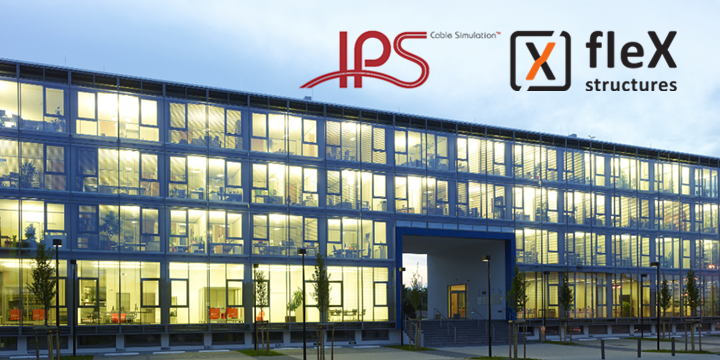
日産自動車株式会社(以下、日産)は、電動パワートレインの開発において「ADVENTURECluster」を核としたデジタルツイン(※)の構築を進め、社会や市場のニーズに迅速かつ的確に対応する基盤づくりを進めています。人材不足・短納期といった相反する状況に対応できるよう、日産はSCSKをパートナーに選定しました。
※デジタルツイン:センサーなどから得た実機データをインターネットやWi-Fiなどを経由してサーバへ収集することで、デジタル空間のデータに情報をリアルタイムに反映する概念やシステム。フィジカル空間(すなわち実機や実地)のデータとデジタル空間のデータが双子さながらの関係になることから、「デジタルの双子」と呼称する。
自動車の電動化における新領域において、デジタルツインを構築する最初のステップとして、日産はSCSKと共同で大規模構造解析ソフトウェア「ADVENTURECluster」を活用した改革を実施しました。現物による試作品を製作する前に、デジタル上で事前検討を進めることで、数百万円の開発費用の削減と約3か月間の開発リードタイムの短縮といった成果を上げることに成功しました。
また次のステップとして、日産はCAE技術を活用した開発体制構築のためSCSKへのアウトソーシングを積極的に進めています。これにより日産は、人的リソースの不足を解消するだけでなく、長年日産が培ってきた“ものづくり”のノウハウと、SCSKのCAE技術力の共創により、持続的なデジタルツインを推進する体制づくりを目指しています。
目次
今回は、日産のものづくりで利用している大規模構造解析ソフトウェア「ADVENTURECluster」の活用状況やその成果と、SCSKが提供するアウトソーシングサービスについて、日産のご担当者様にお話を伺いました。
![]() 日産自動車株式会社 パワートレイン生産技術開発本部 パワートレイン技術企画部 先進パワートレイン技術開発グループ 田口 直人 氏 |
![]() SCSK株式会社 プラットフォーム事業グループ 製造エンジニアリング事業本部 解析ソリューション第一部 秦 瑞希 |
●e-POWERについて
田口氏の部署では、構造解析にかかる時間を短くするために、解析モデルの簡略化や、より少ない部品点数で解析を実施する必要がありました。しかし、モデルを簡略化すると実際の形状とは異なってしまいます。デジタルツインを実現するためには実機形状で解析すること(フルモデル解析or単一部品ではなく、複数部品で解析)が必要であると考えていました。
「社内の他部署の評判がよかったことが『ADVENTURECluster』を導入したきっかけです。今までのCAEソフトでは解析モデルの規模が大きくなると、その分、解析時間が長くなってしまうので、実機形状で解析することを諦めてきました。しかし、『ADVENTURECluster』は規模が大きくても解析が非常に速いので、今まで諦めてきた規模のモデルまで解析ができると考えました」(田口氏)。
日産でどのように「ADVENTURECluster」を活用しているのか。ここでは一例を紹介します。
自動車の電動化で必要となるモーター部品を構成する平角線。日産では、その平角線の曲げ成形解析において「ADVENTURECluster」を使用しています。
●平角線曲げ成形解析の例:平角線を治具に挿入し曲げる工程
「『ADVENTURECluster』によるシミュレーションで、ある程度製作条件の候補の検討をつけることが出来るようになり、従来は3回程度必要だった金型試作の修正が、1回の修正で完了できるようになりました。これが、3カ月程度の工数短縮、金額にして数百万円に相当します。工数短縮できただけではなく、品質もより高まりました」(田口氏)。
※平角線曲げ成形開発日程の例であり、青色部分が試作期間、紫色が実験期間を示します。
加えて、「ADVENTURECluster」の導入により、解析結果から不具合に気付くことができるようになったといいます。ここまでは、「ADVENTURECluster」を導入して日産が得られた効果について説明しましたが、ここからは、CAE技術を活用した開発体制構築のために日産が行っている、具体的な取り組みを2つ紹介します。
日産では、限られた工数の中で、開発・実験に加え、解析作業を行っています。そのため、解析にかける工数が限られており、解析結果をタイムリーに出すことが難しい、と課題意識を持っていました。
そのため、あらかじめ「ADVENTURECluster」でテンプレート化した解析モデルに、決められた条件を入力するだけで即座に解析結果を取得できるようにしました。工数がかかるシミュレーションの解析モデル作成(解析モデルのテンプレート化)はSCSKへ委託、日産は、SCSKが作成するモデルを用い、様々な解析条件での計算や結果の解釈を実施する仕組みを構築することに成功しました。
「シミュレーションを行う際、現物に近い条件設定をCAEソフトで正確に再現するためにはノウハウの蓄積が重要となります。日産でもノウハウの蓄積が急務でした」(田口氏)。
そのため、日産は現物に近い条件設定をCAEソフトで正確に再現するノウハウを蓄積する仕組みを作るにあたり、何もない状態から自分たちで習得するのではなく、必要に応じてSCSKから教授することで効率的に蓄積できるようにしました。
「日産が持続的にシミュレーションに取り組んでいく観点で、全てSCSKにお願いする仕組みにはしませんでした。日産での技術知見を蓄積し、多くの製品テーマで展開していくことを考慮した上で、解析モデルのテンプレート化はSCSKが実施し、その後の様々な条件下での解析や結果の解釈は日産で実施する仕組みに決めました。日産社内でシミュレーションのノウハウが蓄積されるよう、SCSKから技術力の高いノウハウを伝授していただけると考えています」(田口氏)。
●従来のフロー
●現在のフロー
「今回のシミュレーション実践から明らかになった成形条件の組み合せは、RPAを構築して自動的に『ADVENTURECluster』へ読み込ませ、パラメータスタディを自動実施できるように取り組んでいます。シミュレーションを積み重ねることで、データも蓄積されます。それに基づいて感度解析を実施し、条件と結果の因果関係を見ていきます。そのようなプロセスを通し、より最適化された条件で金型や治具製作に取り組めば、さらなる工数削減が見込めると考えています」(田口氏)。
「シミュレーションの可視化や自動化、最適化の部分では、設計空間探索ソフトウェアの『pSeven』も有効活用頂けるのではないでしょうか。『pSeven』の機能である『サロゲート』(数式化・定式化)を用いることで、シミュレーションの工数を大幅に削減することが出来ます」(秦)。
最適化ソフトとの連携に加え、「ADVENTURECluster」による構造解析と、それ以外の電着・塗装やレーザー溶接、樹脂流動、鋳造などのシミュレーションソフトウェアとの連携および連成をすることが非常に重要になってきます。それにより、一段と現物に近い条件設定ができるようになります。
「今後、現実とデジタルをつなぐ、いわゆる『デジタルツイン』を実現するための核として『ADVENTURECluster』が重要な役割を果たすと考えています。『ADVENTURECluster』を核としたシミュレーション技術を活用し、SCSKと共に持続的な『デジタルツイン』の実現を目指していきます」(田口氏)。
(左から:SCSK 今井、日産 田口氏、SCSK 秦、SCSK 南雲)