材料開発にかかる時間とコスト、人的リソースを大幅に削減 MI分野の注目ソリューション「Citrine Platform」
- 材料開発
- MI
- AI
- ../../../article/2023/02/citrineplatform.html
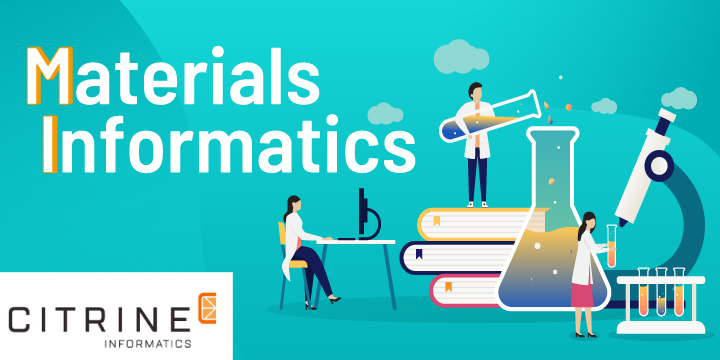
製造業にとって「QCD(Quality:品質・Cost:コスト・Delivery:納期)改善」は、常に取り組んでいるテーマの1つです。その中で、モノづくりの“前工程”である設計段階での品質を高め、全体のコスト削減・期間短縮を目指す「フロントローディング」が進んできました。ここで、重要な役割を担ってきたのがCAE(Computer Aided Engineering)です。
そのCAEにも課題はあり、それらを解決するものとして登場したのが、機械学習・AIを用いた「サロゲートモデル」です。設計プロセスを大きく効率化するものとして期待されていますが、具体的に何ができて・何ができないのか。また、どのような効果があるのでしょうか。今回は、製造業務のデジタル化を進める(デジタルマニュファクチャリング)ツールを担当しているSCSKの3名にインタビュー。さらに深層学習によってサロゲートモデルを3Dデータにも対応させることで、活用の可能性を大きく進めた3Dサロゲートモデルの最先端技術についても、詳しく聞きました。
目次
![]() SCSK株式会社 プロダクト・サービス事業グループ デジタルエンジニアリング事業本部 プロダクト技術部 第三課 佐藤 充 |
![]() SCSK株式会社 プロダクト・サービス事業グループ デジタルエンジニアリング事業本部 プロダクト技術部 第三課 渡部 和帆 |
![]() SCSK株式会社 プロダクト・サービス事業グループ デジタルエンジニアリング事業本部 プロダクト技術部 第三課 澁川 京香 |
―― 最初に、製造業を取り巻く現状と、CAE活用の課題について伺えますか?
佐藤 製造業では多品種・少量生産が進んだ上、開発サイクルが短期化していることもあり、競合よりいかに早く・低コストで新しい製品を投入するかが大きなテーマになっています。「設計段階でコストなどの8割が決まる」とまで言われるように、フロントローディングの重要性はますます高まっています。なるべく手戻りがないように、また製造プロセスまで考慮してコストを低減できるように設計することが求められ、そのために使われてきたのがCAEです。
しかし、CAEを使うには専門知識が不可欠で、ツールがあれば誰でも使いこなせるものではありません。
渡部 そのため多くの企業では、設計とCAEは別のメンバーが担当しています。まず、設計担当からCAE担当にシミュレーションを依頼し、CAE担当が計算し、結果をまとめたレポートを設計担当にフィードバックするという流れです。CAEで1つの形状の強度をシミュレーションする場合、一般的に数時間から数十時間かかります。シミュレーションに加えて一連の作業に時間がかかる結果、依頼からレポートをもらうまで数日かかってしまいます。これでは、近年の開発サイクル短縮に対応しきれないと課題になっています。
―― 設計者自身がCAEを使っているわけではなかったのですね。
佐藤 もちろん、設計者自身がCAEによるシミュレーションまで担当できればベストです。しかし、設計者の業務は非常に多岐にわたっており、ツール毎に専門知識が必要な専任者向けのCAEまでも勉強して自分で対応するのは難しい状況です。いわゆる設計者CAEの領域も広がってはいますが、その機能は限定的です。CAEの進歩により、更に大規模で複雑な現象が取り扱えるようになっている分、より専門性も高まっているとも感じます。
設計者とCAE担当者が異なる現状では、シミュレーションの結果がうまく活用できないケースもあります。例えば、「シミュレーションの結果、強度が足りないため、厚みを増やすべき」というレポートが戻ってきても、設計フェーズの進捗やコスト的にそれは難しい、ということも少なくありません。
このように設計上の課題が見つかっても、現実的な解決策を考えるために時間がかかることから、「CAEの計算時間を速くしたい」「設計プロセスを短縮したい」といった要望は多くの企業からいただいていました。
―― サロゲートモデルは、こういった課題をどう解決するのでしょうか?
佐藤 サロゲートモデルは、データから法則やパターンを発見して、未知の結果を予測するモデルです。CAEが物理学をベースにしていたのに対して、サロゲートモデルは統計学に基づく機械学習がベースです。物理学の複雑な方程式で現象をすべて解くCAEに比べ、機械学習で条件と結果の関係性を導くことで途中の計算を省略できるサロゲートモデルは、同じ結果にたどり着くまでの時間を圧倒的に短くできます。
(出典)最適化/機械学習による設計空間探索ソフトウエア pSeven: Predictive Modeling(予測モデリング)|SCSK株式会社
最近では、製造業以外でも機械学習を用いた事例を多く聞くようになりました。例えば、売上予測では過去の天気や気温、販売実績などのデータを学習してパターンを導き、未来の売上を予測しますが、設計におけるサロゲートモデルもそれと似たイメージです。製品の形が決まっている場合、「どこに力をかけた時にどれくらいのダメージが生じる」といった、過去の実験やCAEのシミュレーションによるデータを多く集めてモデルを作成し、製品形状や生産工程を変更した際の結果を予測します。物理方程式を解くのではなく、形状に対する結果のみを計算することで、従来のCAEによる計算に比べて予測にかかる時間を大幅に短縮できるようになりました。SCSKでもサロゲートモデルを採用した製品を7~8年ほど前から扱っており、大手製造業を含む先進的な企業では研究などで、限定的に活用されています。
―― これまでサロゲートモデルがあまり普及してこなかった理由はどこにあるのでしょうか?
渡部 サロゲートモデルでは一般的に応答曲面法を用いており、形状や寸法をパラメータ(数値)化して解析するため、寸法の数や部位が変わるとモデルを作り直さなければなりません。また、見た目や形状の変化など、数字で表現しづらいところは学習できないという課題がありました。このような予測できるモデル形状の制約から、従来のサロゲートモデルでは活用領域が限られてしまいます。こういった課題を解決するものとして、今、注目されているのが、3Dサロゲートモデルを生成する「Neural Concept Studio(以下、NCS)」という製品です。
―― NCSはどういう製品なのでしょうか?
佐藤 NCSはDeep Learningと画像認識技術の応用によって3D形状と分布データをそのまま学習し、3Dのサロゲートモデルによって予測を行うツールです。Deep Learningは機械学習の一種ですが、特徴量を自律的に抽出して学習するため、事前にパラメータを設定する必要がありません。画像認識などに多く用いられる技術で、AIが膨大な動物の写真から自動で犬や猫などの特徴を学習し、動物の種類を正しく判別する事例を見たことがある方も多いのではないでしょうか。写真のような2次元の画像を扱う際ではConvolutional Neural Network(CNN)という技術を用いますが、NCSではGeodesic CNNと呼ばれる技術によって3次元の形状を学習します。
これにより、従来のサロゲートモデルとは異なり、教師データとして定めた寸法の数や部位にとらわれず、3次元の形状をAIモデルの学習に適用できるようになりました。設計データをパラメータ化する必要はなくそのまま学習に利用でき、自由な3次元形状に対して分布データを予測できます。また、予測結果もパラメータとしてではなく分布図として得られるため、ぱっと見て分かりやすいです。そのため形状データさえあれば設計者自身がNCSを使って予測できるようになり、これまでと違ったアプローチが可能になります。
―― 具体的にどういったことができるようになるのでしょうか?
渡部 指定した寸法の延長線上にないものや、寸法として表すことが難しい形状もまとめて学習でき、予測の幅が広がります。例えば、世代の異なる自動車の形状を合わせて学習させた1つのサロゲートモデルを作成し、同じモデルで幅広い設計データに対応できる、といったイメージです。しかも、予測自体は数秒程度で完了するので、より多くの設計アイデアを検討することができます。
―― AIでは、予測精度が問題になるケースもあるようですが、NCSではどうなのでしょうか?
渡部 確かにそういった問題もありますが、そもそも100%の精度は求められませんし、これはCAEでも同じです。最終的には実験などで確かめることになります。しかし、NCSによって一定の精度で予測し、有力な設計モデルを絞りこむことによって、無駄なシミュレーションや実験を減らすことが期待できます。
佐藤 NCSは、予測する際に教師データとの類似度から予測信頼性を数値化します。この数値が高いほど予測の精度が高いと言えるため、数ある設計の中から、どれがよさそうかを定量的に判断できます。こうして絞り込んだ上で、CAEでシミュレーションを行うといった流れになります。
―― CAEが不要になる、というわけではないのですね。
澁川 CAEを使わなくなるのではなく、設計とシミュレーションのプロセスが大きく変わるというイメージです。これまでは、設計した後にCAEでシミュレーションを行うというセットを何度もループさせ、1つのループに数日かかっていました。これに対して、NCSでは設計者自身である程度の予測まで実施でき、しかも数秒で結果が出ます。設計作業の一環としてシミュレーションできるようになり、ある程度絞ってからCAE担当者に依頼できるようになります。CAEや実験にいたる前の設計段階を効率化・高品質化することによって、海外ではリードタイムを90%以上も短縮できたという事例も報告されています(※)。
―― 導入はどのように進めるのでしょうか?
佐藤 まず、お客様がお持ちの実際のデータを用いたPoCから始めることをお勧めしています。テーマに対して、どのようなデータがどれくらい必要かの推測・検討などからSCSKがサポートします。
―― データの準備が大変なのではないでしょうか?
渡部 データ数がネックというお客様も少なくありません。ただ、CAEのシミュレーション結果のほか、実験の結果も投入するなど、活用できるデータはさまざまあります。また、教師データとなるCAEの計算を自動化するツールや、データを揃えるための方法をSCSKから提案・アドバイスすることも可能です。
―― 最後にNCSの魅力をまとめるとどういった点になりますか?
渡部 類似のツールは他にもあるのですが、NCSは流体解析、電磁場解析、構造解析、プロセスシミュレーションなど、さまざまな種類のシミュレーションに1つのツールで対応できることが最大の強みではないでしょうか。
澁川 つまり、全社的なシミュレーションをNCSにまとめられるということです。CAEでは分野ごとに担当者が分かれていましたが、NCSでは1人ですべての解析分野のモデル作成を担当できます。そして、そのモデルを使って設計者は容易にシミュレーション同等の予測を得られます。もちろん、モデル作成は専門知識が求められますが、NCSではかなりハードルが低くなっています。人材確保が難しくなる中で有効なツールで、分野や部署をまたいでシミュレーションを集約できるということは、新しい組織の形にもつながると思います。