メタバースで製造業が変わる!NVIDIA Omniverseセミナー
- イベントレポート
- メタバース
- DX
- ../../../article/2022/10/omniverse.html
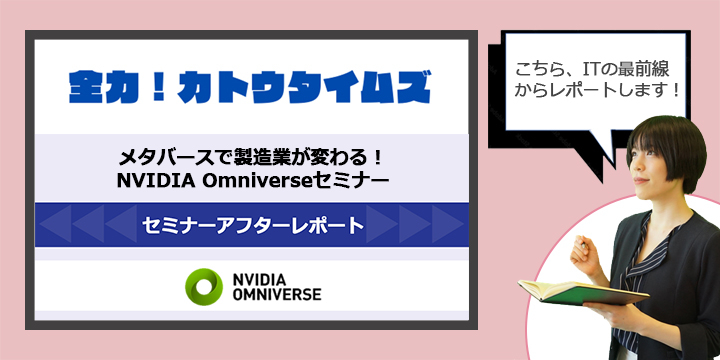
現実世界の空間や設備・物を、デジタル空間上に“双子”のように再現するデジタルツイン。この最先端の技術で、工場の製造ラインをデジタル空間に再現しようと取り組んでいるのがトヨタ自動車株式会社(以下、トヨタ自動車)です。ロボットの動作や、製品の物理的な動きまでを再現できれば、製造の現場が抱える労働環境と品質の問題を解消するだけでなく、エンジニアリングチェーン全体をドラスティックに変えることになると期待されています。
SCSKによる全面的なサポートを受け「NVIDIA Omniverse」を導入、プロジェクトの現状から未来まで、その挑戦について詳しく伺いました。
![]() トヨタ自動車株式会社 素形材技術部 鍛圧・焼結・樹脂成形技術室 1グループ長 鈴木 一広 氏 |
![]() SCSK株式会社 プロダクト・サービス事業グループ 中部関西プロダクト・サービス事業本部 ITエンジニアリング部 部長 輔田 健大 |
![]() SCSK株式会社 プロダクト・サービス事業グループ 中部関西プロダクト・サービス事業本部 ITエンジニアリング部 第一課 吉田 孝志 |
目次
―― デジタルツインに取り組むこととなった背景について伺えますか?
鈴木氏 私は自動車製造において、アルミの塊をつぶして部品の形に成形するアルミ鍛造ラインを担当しています。モノづくりにおいて現地現物の考え方は非常に重要で、データに頼らず五感をフルに生かすことが、課題の本質を見極めることに直結します。一方で、何が何でも現場に行けばいいというものではなく、安全を確保し現場で高技能を発揮することに集中できる環境づくりを進めることを命題と感じています。
鍛造ラインも環境温度が高く、潤滑液が蒸発した煙も出ているなど、比較的「3K(きつい・汚い・危険)の職場」であり快適な場所ではありません。アルミ鍛造品の製造ラインは、550℃くらいに熱せられたアルミ材料を搬送し、金型に入れ、5,000トンもの強い荷重を加える工程を何度も繰り返す非常に危険な現場です。また、同じ荷重をかけても1ミリ単位の誤差が出るため、個体差のある製品でもロボットが正確に運搬できるよう「ティーチング」と呼ばれる微調整も欠かせません。
そのために、生産準備中は人が数カ月の間、何度も工場に入り、ロボットのティーチングを行っていますが、この回数や滞在時間を減らしてより高技能を発揮できる働き方へ改革していきたい、そう考えたことが、デジタルツインに取り組むことになった大きなきっかけです。現場の作業すべてを再現できなくても、事前のシミュレーションだけである程度ティーチングできれば、工場内での人の作業は減らすことができ、最後の短時間の造り込みに集中し、より完成度を上げることができます。
―― この課題を解決するために、デジタルツインに注目した理由はなんだったのでしょうか?
鈴木氏 これまでも、CADを使って生産ラインや工場全体を3Dモデル化し、安全上問題ないか、設備の配置が干渉しないかなどのシミュレーションを行っていました。しかし、ティーチングとなると単に形状を再現するだけでは足りず、慣性を考慮したロボットの動き、製品の重さや摩擦などの物理現象まで正確にシミュレーションできる環境が必要です。それを実現するには、現実の世界を双子のように再現するというデジタルツインのような環境が不可欠だと考えました。
SCSK 吉田 SCSKでは、鍛造プロセスの解析を行う「TRANSVALOR MATERIAL FORMING」を含めたCAEなど、デジタルエンジニアリングの領域で以前よりサポートを行ってきました。その中で今回の課題について話を伺う機会があり、ちょうど2020年から取り扱いをはじめたメタバースプラットフォーム「NVIDIA Omniverse(以下、Omniverse)」を活用して実現できるのではと提案しました。長年ロボット設備も手がけてきた知見もあり、実際にOmniverseにロボットの動きなどを組み込み、「こういうことならできそうだ」とお見せするところからはじめました。
鈴木氏 第一印象からかなり良かった記憶があります。トヨタ自動車では、3年前からデジタルで世界一を目指す目標を打ち出し、最新技術をより積極的に活用するようになりました。特にデジタルツインのような領域は日進月歩で進化するため、モタモタしているのが1番よくないと考えています。デジタルの最先端をいくSCSKと連携することで、大きく進められると感じましたし、まずはやってみた方がいいとスタートすることを決めました。
―― Omniverseの印象を詳しく教えていただけますか?
鈴木氏 まず質感などがとてもリアルだなと感じました。デジタルツインで高精度なシミュレーションを行うためには機能面においてリアリティが重要なのは言うまでもありませんが、それだけでなく、人の心を動かせるという点でも重要です。というのも、デジタルツインは最終的には現場で作業する技能系の社員が利用します。使う人を増やすには、心を動かしてそれをやりたい・使いたい・使う価値があると思ってもらえるかどうかにかかっています。そのためにも没入感は大切で、最終的にはリアリティの追求になると考えていました。
実際、他部署と情報交換している時にも、Omniverseのデジタルツインを見せると、自分も触ってみたいと言われることが多いです。それだけ響くものがあるのだと思います。
―― 確かに、デジタル上に再現したと言っても、リアルさがなければ、活用に前向きになれないところがあるのかもしれません。そのほかOmniverseのメリットはどういったところにあると思いますか?
鈴木氏 Omniverseはただのシミュレーションソフトではなく、複数の技術を統合できるプラットフォームという位置づけであり、ここがほかのツールにはない特長です。Omniverseは異なる種類のデザインソフトウェアやCADのデータを一元的に可視化し、各々のツールで行った修正もリアルタイムで反映できます。そこで、さまざまな情報をすべてOmniverseに統合し、関係者全員で共有する未来を描けると考えました。
例えば、Web会議で決まった変更点も、今は1度持ち帰って設計者がCADで修正し、1ヵ月後に再度集まって専用のビューワーツールを使ってレビューするしかありませんが、Omniverseであれば、Web会議中にデジタルツイン上で変更を反映し、その場で試すことができます。これができれば、製造ラインに関する工程を大きく短縮し、進め方が根本的に変わる未来もあるはずです。
(出典)NVIDIA
SCSK 輔田 さまざまな情報をすべてOmniverseに統合してデジタルツインに再現する、この理想形を実現するには、製造ライン全般について理解して進めなければなりません。SCSKはCADやCAE、ロボットなどエンジニアリングチェーン全般のツールを扱っており、それぞれスペシャリストが揃っています。また、CGによるビジュアライズを得意とするメンバーもおり、製造ラインに関する知見からビジュアル面までトータルで支援できることが強みです。
鈴木氏 製造ラインの事情などをある程度把握した上で、進めてもらえるのはやはり頼もしいです。
―― 現状、どこまで実現できているのでしょうか?
鈴木氏 2022年末のOmniverse導入から1年経った現在(2023年12月)、物理シミュレーションは思った以上にスムーズに実現できました。
トヨタ自動車には「からくり」と呼ばれ、電気などの動力を極力使わず、治具の工夫で動かす仕組みで製造現場を改善しようという取り組みがあります。例えば、鉄の棒がレールで流れてくる際、1本ずつピックアップするためにすき間が空くように調整するといった仕組みですが、その機構はOmniverseでの再現に成功しました。次は、「力を加えて掴む」といったロボットの動きをOmniverse内にどう再現するかに取り組んでいるところです。そのために「ADA」サイクルによる、現実とデジタルツインとの双方向の連携を目指しています。
―― ADAとは何でしょうか?
鈴木氏 ADAとは、Actual(現実)、Digital(デジタル)、Actual(現実)の頭文字を取ったものです。これまで培ってきた現場のノウハウをデジタル化した上で、デジタル上で70点程度までの完成度までPDCAを回し、その成果を現場にフィードバックすることで、人が100点を目指し完成させるという働き方のサイクルです。
―― 治具とは違うロボットシミュレーションならではの難しさはあるのでしょうか?
SCSK 吉田 通常、工場内ではロボットをコントローラで動かすのですが、それをデジタルで再現するにはプログラミングが必要です。具体的には、専用のRobot Operation System(ROS)というソフトウェアを利用しますが、現場にはその知見を持つ人が少ない上、ロボットメーカーごとにコントローラが異なるため、個別にトレーニングしなければなりません。その解決策として注目しているのが、READY Robotics社の「Forge/OS」というツールです。これはロボットメーカー(コントローラ)の違いを問わず、Omniverse上のロボットと実機ロボットを同じコントローラで動かせるというもので、“使える可能性”があるのではと検証を進めている最中です。ROSからコントローラへの変換が不要になるうえ、ロボットメーカーの違いを超えてあらゆるロボットをOmniverse上でプログラミングできるという点から、汎用性を持って利用できると期待しています。
(参考)本取り組みに関するREADY Robotics社のプレスリリースはこちら
鈴木氏 次々出てくる課題をどう乗り越えるのか、一緒に挑戦してくれるのは本当にありがたいです。現状は、まだ全体の1合目に届いたかどうかといったところですが、最初はなかなか進まなくても、徐々にスピードアップしていくのがセオリーです。完璧な理想形ではなくても、半年以内には実際の現場で利用開始できるのではと考えています。
―― さらにその先の理想形としては、どういったものをお考えでしょうか?
鈴木氏 実現したいこととしては、機械学習を活用したトレーニングの自動化があります。実際の工場では、ロボットが少し揺れたり、アルミ鍛造で製品に誤差が出たりと、さまざまなバラつきが出ます。こういったバラつきまでもデジタルツインで再現できれば、そのデータを強化学習で分析し、最適化に向けたトライアンドエラーまで自動化できるのではないか、と考えています。強化学習を使って、週末のうちに最適化をある程度まで終わらせて、週明けに出社したら一定精度のモデルができている。そんな未来も十分あり得るでしょう。
鈴木氏 Omniverseでの取り組みは、他部署からも非常に注目されています。現場ごとに色々な苦労があるので、アルミ鍛造ラインからほかのラインに、さらには全工場にも広めていけたらいいですよね。ここでも、Omniverseが統合プラットフォームであるという点は強みです。
「デジタルで世界一を目指す」といった時に、人が苦労しているところを最先端のデジタル技術で改善できないか、「魅力的な職場を作る」ためにデジタルを活用して何ができるのか、と常に考えています。今後も、さまざまな取り組みを進めたいと考えています。
SCSK 輔田 魅力的な労働環境づくりをデジタルの面で支援することができ、我々SCSKとして大きな意義を感じています。
Omniverseはビジュアルのリアルさはもちろん、機能単体ではなく、統合プラットフォームとして、CAEの結果を取りこむなど、さまざまな活用が可能です。複数の関係者がデジタルツインを一緒に見て確認することで、業務改善にもつながるでしょう。4月からは専任の支援スタッフを増やし、体制を強化していく予定です。SCSKの人と技術ノウハウ、幅広い開発実績を総動員し、鈴木様の素形材技術部からトヨタ自動車全社、そして世界へと夢を広げる支援を行っていきます。