生産管理システムと
WMS(倉庫管理)システムの連携
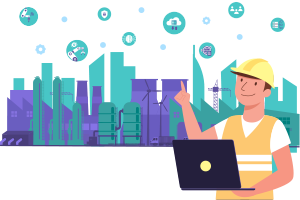
1. WMSの役割と概論
WMS(倉庫管理システム)は、現在ではかなり一般的となり多くの企業で導入されている。通常は基幹システムとのデータ連携のもとに導入・使用されるが、BIツール的にデータの受け渡しのみを行いながらスタンドアローンに近い状態で使用される例もある。
倉庫・荷役管理においては「ロケーション管理」「先入れ先出し管理」「在庫量・回転率管理」等が欠かせない。保管効率及び倉庫内の荷役効率をある程度の水準に保とうとすると、人の記憶による属人的な運用ではすぐに限界が出てしまう。荷役効率管理として人時生産性等を取得できる仕組みなども、殆どのツールで標準的に運用されている。
なおWMSは、物流全体の管理ツールとしてTMS(配送・運行管理システム)と併せて運用されることも多い。両者の機能概要を図に示す。
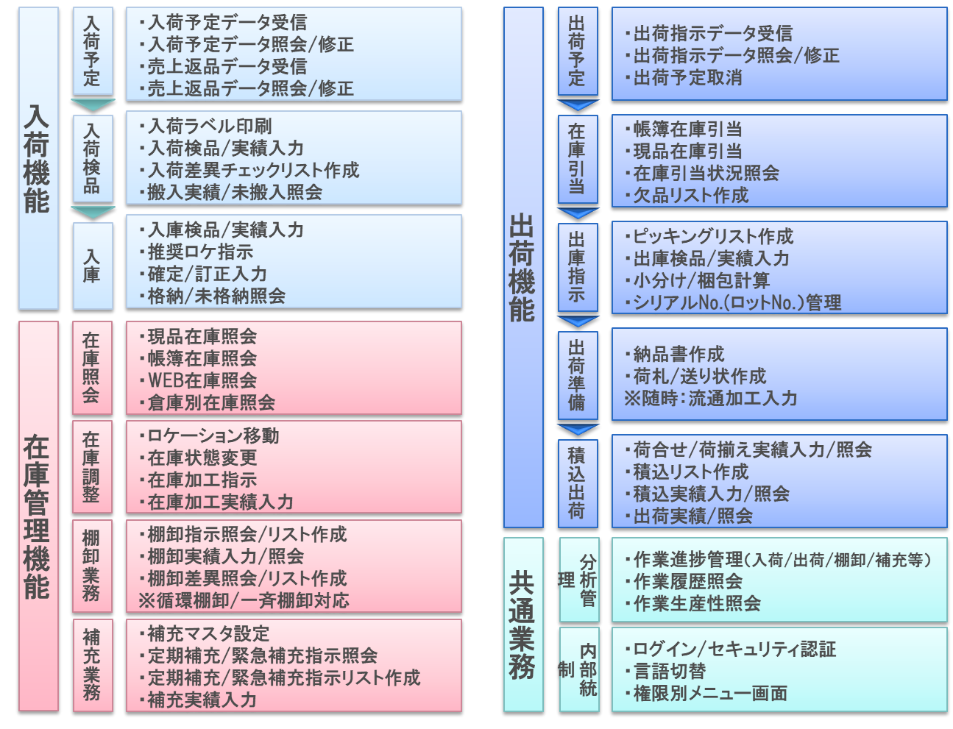
2. WMS導入の際の一般的な課題
本稿では生産管理システムとの連携という視点でWMSの役割を述べるので、ここでは工場倉庫を想定する。WMSを導入する際に考慮すべき点は以下である。
- 管理単位(アイテム・SKU・部品の枝番・半製品仕掛品等)
- ロット管理の有無・必要性
- 先入れ先出し管理の有無・必要性
- 棚卸しの頻度(循環棚卸し等を想定すべきかどうか)
- 入荷・出荷それぞれの情報更新タイミング(リアルタイムか、定時登録か)
- ロケーション管理・ピッキングの方式
例:ハンディターミナルを用いた人手によるピッキング・整品単位でトータルピッキングも可能とする・ロケーション表示はバーコード 等 - ピッキングの指示順番ロジック
- 在庫量・在庫回転率等の表示有無 等
重要なのは、実務に必要な機能をもれなく盛り込むことに加え「マネジメントとして行いたいことは何か」までを想定することである。例えばピッキングを生産性管理してスムーズに行いたい場合、場所別の人時生産性取得機能等が必要となる。導入するためのコストとの見合いで、仕様やパッケージを定める必要がある。
3. 生産管理システムとの連携留意点①通常の倉庫管理
さて、ここからはWMSと生産管理システムとの連携パターン並びに留意点を考えていきたい。工場倉庫と言ってもいくつかのパターンが想定されるので、以下の表でそのポイントを整理する。
荷役管理 | 保管・在庫管理 | |
製品倉庫 | ラインアウトされた製品の搬入出・工数管理 出荷指示・出荷工数管理 |
製品倉庫管理に必要な機能(ロケーション・入荷格納指示・出荷指示・ピッキング順指示等) |
部品・半製品倉庫 | 生産管理システム上で必要とされる数量の入荷・払い出し指示とその工数管理 BOM上で示された必要部品の所要量在庫管理 等 |
部品倉庫管理に必要な機能(単品別在庫数・ロケーション・入出荷指示、ピッキング方式およびピッキング順、指示~供給L/T管理など) |
資材備品等の倉庫 | 同様に生産管理システムで必要とされる資材の搬入指示とその工数管理 | 資材管理に必要な機能(概ね上記と同じ) |
製品在庫のみをWMSで管理するのであれば、生産管理システムとの連携については余り神経を使う必要はない。完成品が払い出しされるタイミングと、その際に必要な保管場所・荷役工数等を指示できれば、多くの場合は事足りる。ただし、製品倉庫が外部倉庫である場合、横持ちが必要となるのでその手配は機能として必要になる(TMSの併用も必要となる場合がある)。
部品・半製品・資材管理などを生産管理システムとWMS横断で行おうとすると、要件は少々複雑となる。日常の供給・搬送指示はもちろんのこと、月次・週次等の生産計画サイクルに基づいて必要な部品・資材等の所要量を算出し、日単位でWMSを経由して入出荷の指示を与える必要がある。この場合はWMSと生産管理システム(或いは基幹システム)をある程度シームレスに繋ぐ必要が出てくると考える。
また部品等の場合は「指示を行ってからどのくらいの時間で使用可能となるか」という想定も必要である。特に工場倉庫で部品や資材のみを近隣の外部倉庫に保管していると言うパターンは結構多いので、横持ちのリードタイムやタイミング等も考慮する必要が出てくる。
4. 生産管理システムとの連携留意点②ラインサイドへの部品等供給
3をさらに推し進めると、いわゆるJIT生産・同期生産等を行っているラインにおいて、製品・部品等をどのタイミングでどのラインに供給すべきか…と言うマネジメント課題が出てくる。
多くの生産管理システムでは必要な部品数や種類の指示は出来ても、納入タイミングの指示までは行えない。このため、どの部品や資材を「何時にどこに」届けるか…と言う精密な指示をWMSベースで行なう事が必要となる。
当然、在庫管理はリアルタイムでなければならないし、各在庫場所からラインサイドまでどのくらいの時間がかかるかについても「最低限時間単位(可能ならば分単位)」で管理できなければならない。生産管理システムとWMSがリアルタイムで情報連携を行える必要があり、必要な仕組みの構築は相当高度になるが、使い方によっては大きな効果を見込める。
実際大手企業でこのような仕組みを構築した事例を見てみると、部品や資材倉庫を工場周辺に集約し「TC(トランスファーセンター)」として運用する例が一般的である。上記のような複雑な仕組みにおいて、在庫が各所に分散してしまっていては管理がほぼ不可能になるので、在庫を一箇所に集めると言う設計が合理的であると考えられる。
5. 生産管理システムとの連携留意点③サプライチェーン上の在庫把握
最後は1工場にとどまらず、サプライチェーン上の各所の在庫を可能な限りリアルタイムで把握し、原材料・仕掛品・製品在庫全体の最適化を図るというアプローチである。図にそのイメージを示す。
実際のものの動きと情報ステータス(止まっているのか・動いているのか・次どこで使われるのかなど)を連携し、サプライチェーン全体で各プレイヤー間の意思決定・意思疎通をスムーズにするイメージである。
サプライチェーンへのWMS展開で考慮すべきは、以下の3点である
- そもそもサプライチェーン全体の在庫を見える化することの意義
- 取引先と情報共有することの難易度、およびそのメリット
- 情報連携によるメリットの分配方法
要するに在庫が適正化できるか・コスト削減に繋がるか…と言うことである。見える化によってミルクランや共同集配、或いは製品在庫の低減・欠品率向上と言った効果にどれだけ結びつくかどうかを十分に検証した上での導入が望まれる。
6. 終わりに
WMSもかつての大型一辺倒のパッケージから、クラウドを中心とした安価なモデル・機能別に特化したモデルなどが登場してきている。各企業のニーズに合った導入を検討することは十分に可能であろう。
システムの連携は手段に過ぎない。大事なことは「連携が出来ること」ではなく「連携によって何が良くなるか分かること」である。この点を常に忘れないようにしたい。
- 執筆者
-
- 株式会社日本能率協会コンサルティング
- 生産コンサルティング事業本部 サプライチェーン革新センター
- シニア・コンサルタント 広瀬卓也
-
- 株式会社日本能率協会コンサルティング
- 生産コンサルティング事業本部 サプライチェーン革新センター
- コンサルタント 刈谷優孝