ユーザー事例
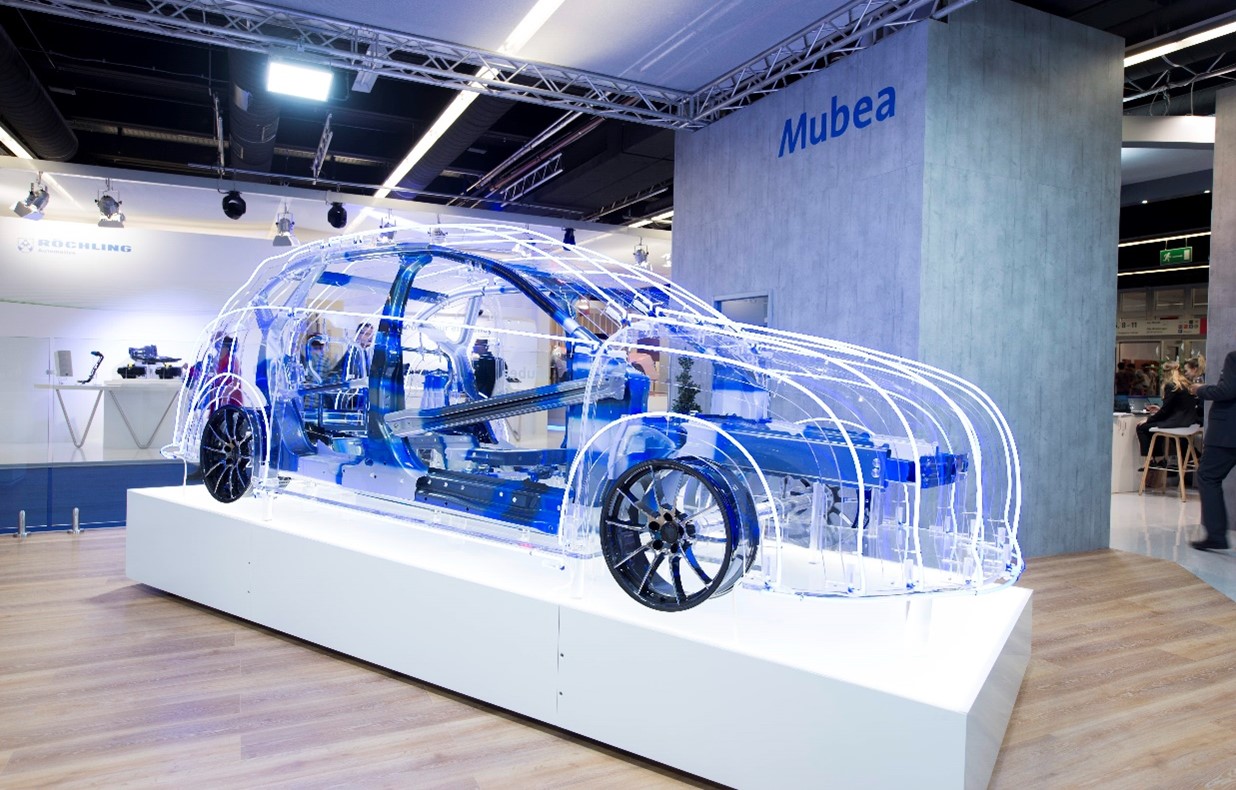
自動車の電動化における設計課題解決: 軽量で耐衝突性の高い自動車、そして革新的なAIソリューションの役割
自動車の完全な電動化へのトレンドは、チャンスであると同時にチャレンジでもあります。排気系などのドライブトレインの特定の要素が姿を消すことになる一方、バッテリーのような部品は、現在普及が進んでいます。
自動車軽量化のための革新的なソリューション
Mubeaは、自動車産業における国際的なパートナーであり、革新的な軽量化のスペシャリストです。家族経営のオーナー企業として、長期的で持続的な成功を収めている企業の代名詞にもなっているMubeaは、ドイツ・アッテンドルンに本社を置き、世界20カ国、45カ所に拠点を持つグローバル企業でもあります。
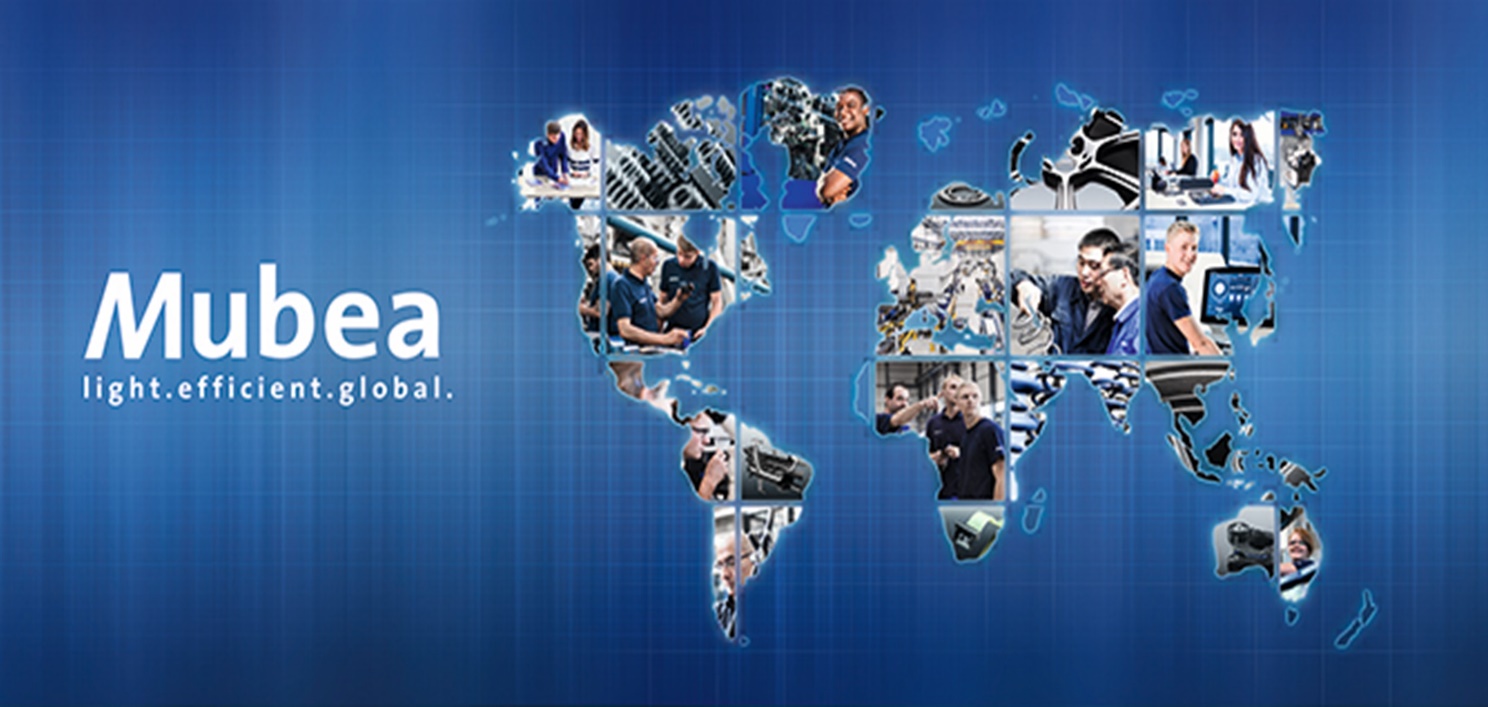
Mubeaグループは、軽量化コンポーネントの革新的な開発と生産をコアコンピタンスとし、従来型および電動化ドライブトレインによる自動車ビジネスの成功に貢献しています。さらに、Mubeaは、他のモビリティ分野、特に航空産業においても、その中核となるノウハウを確立することに成功しています。
数十年の間に、Mubeaはシャーシ、ボデー、パワートレインの各製品を提供する自動車業界のTier1サプライヤーのトップに成長しました。提供される製品そのものと同様に、その製品開発プロセスもまたユニークでカスタマイズされたものです。Mubeaの設計は、重量、信頼性、コストなどの相反するすべての要件の間で最適な妥協点を見出すために、設計の探求を重ねた結果生まれたものです。
Dr. Niklas Klinke(Team Lead - Engineering Tools and Methods, New Body Development)は、以下のように話しています。
「Mubeaでは、お客様のニーズに合った製品構成を見つけるために、設計最適化技術の活用を進めており、そのプロセスでは、有限要素法解析(FEA)を利用しています。設計案は、特別なCAEプロセスチェーンに基づき自動的に評価されます。メタモデルベースの最適化により、最適な部品形状や厚み分布を求めます。
これまでの手法は、最大変位や力などの主要な結果をスカラー値として抽出し、本格的なFEA解析を必要とせずに設計を迅速に評価できる予測モデルを作ることでした。この方法は、ほとんどの場合において非常に有効でしたが、現在はさらにNeural Concept Shapeを使用することで、以下のようなことが可能になりました。
- 1. 単一の重要な結果だけでなく、完全なモデルの挙動と基礎物理を利用する
- 2. 古いプロジェクトの過去のシミュレーション結果を活用し、モデル学習の労力をさらに削減する」
このホワイトペーパーでは、Mubeaが以下の課題にどのように取り組んだかを紹介することに重点を置いています:
- 与えられたデータセットに対して、3次元場の応答を予測する方法
- 設計者が使う可能性のある設計検証ツールの考え方
- Mubeaの蓄積された知識・経験を、格納されているデータの面からどう生かすか
下図は、バッテリーハウジングの代表的なデザインです:
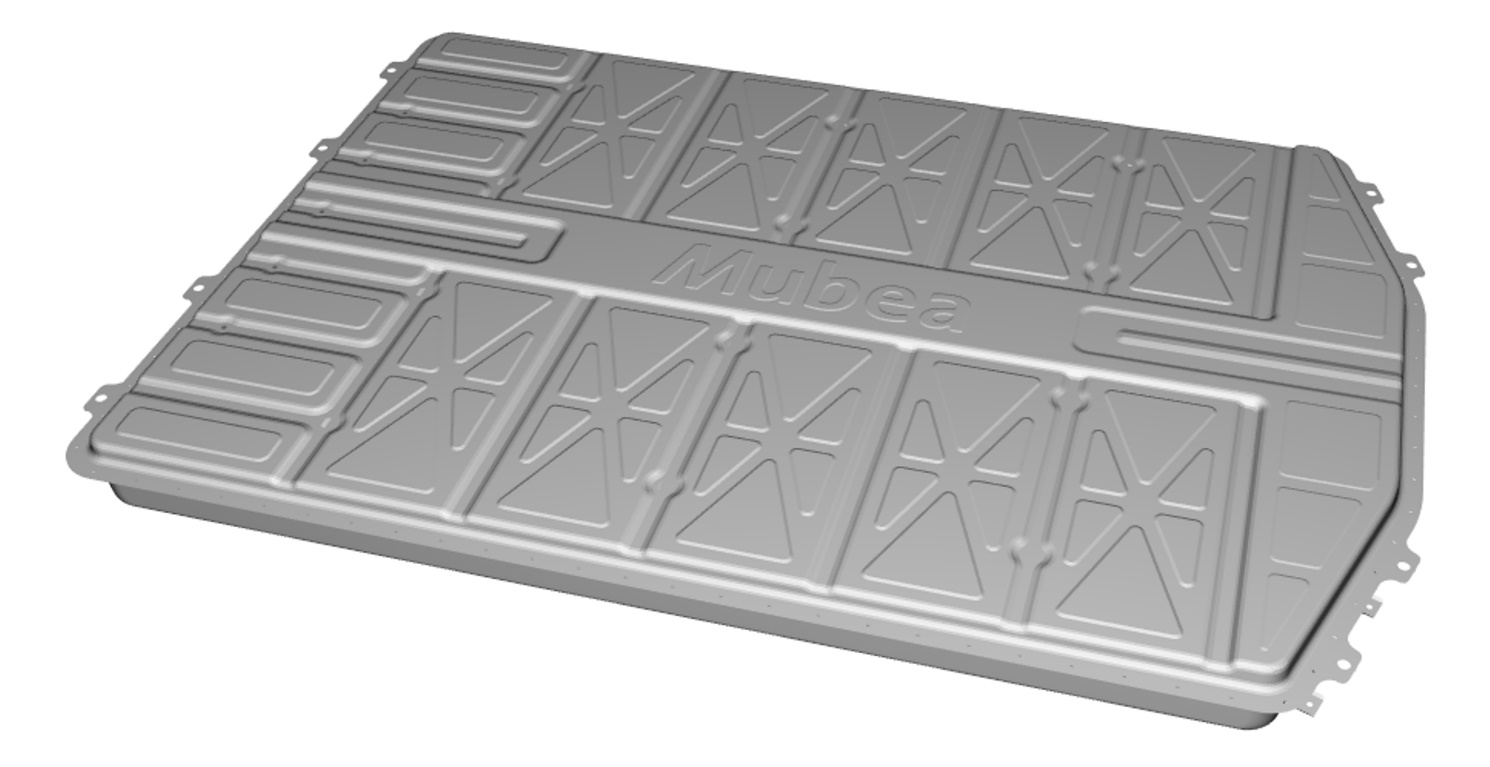
図1: バッテリーハウジングの代表的なデザイン。
革新的なプロジェクト:ミッション
Neural Conceptは、エンジニアの作業時間を短縮しながら、抜本的な設計改善へと導くことをミッションとしています。今回は、EV用バッテリーハウジングの設計において、MubeaとNeural Conceptがどのように協業してきたかを紹介します。このホワイトペーパーで紹介するのは、深層学習のアプローチをとるNeural Concept Shape(NCS)です。これは、CADや3Dシミュレーション(CAE)などの企業データを活用しAIベースのアプリを作成することで、社内のすべてのエンジニアが準リアルタイムにシミュレーション結果を得られるようにするソリューションです。
設計エンジニアにとって重要なのは、自動車の側面衝突時においてもバッテリーの構造的な完全性が保証されている設計案かどうかを検証することです。そのため、軽量化やパッケージングの要件からくる数百の設計オプションについて、この機能要件の観点から検証する必要があります。
革新的プロジェクト:実行
このプロジェクトでは、バッテリーハウジングのサイドレールがバッテリーに接触しないことを保証することが課題でした。一般的な方法では、接触力の構成要素間の距離のいずれかを測定するレポートテンプレートを作成することです。
「レガシーアプローチでは、接触力がゼロになるように設定し、厚みの最適化を行いました。しかしこのアプローチのモデルの品質は、非線形性やゼロ近傍の応答の不安定性のため、非常に悪いものでした。そこで、3次元変形を予測し、その場における距離や衝突を計測できるようなソリューションを探しました」。
そのため、Neural Conceptチームの課題は、準リアルタイムで動作するAIベースのアプリケーションを構築し、単純化したアプローチにおいても要点を外すことなく、設計者に答えを与えることができるようにすることでした。最も重要なのは、衝突シミュレーションの際に、特定の設計構成がバッテリーの接触を引き起こすかを予測できるようにすることです。信頼性の指標としては、「偽陽性」がないこと、つまり実際には接触がないのにアプリが接触を予測するケースがないことや、「偽陰性」が最小であること、つまりアプリが接触状況をハイライトするのを見逃す状況などが最小になることが挙げられます。
このアプリに入力された何百もの設計に対して、基盤となるソフトウェアのNeural Concept Shape(NCS)が予測した偽陰性は1件のみで、偽陽性は発生しませんでした。これは最も重要なことで、このサロゲートモデルを使用して、バッテリーハウジングの設計を最適化することができます。
XYZ変位と最大力の予測品質について、より詳細な分析が行われました。基盤となっている予測エンジン(NCS)の精度を測る公正な指標として、いわゆる決定係数R2があります。サロゲートモデルは非常に高い精度に達し、表1に示すテストセットでのR2スコアは以下の通りです:
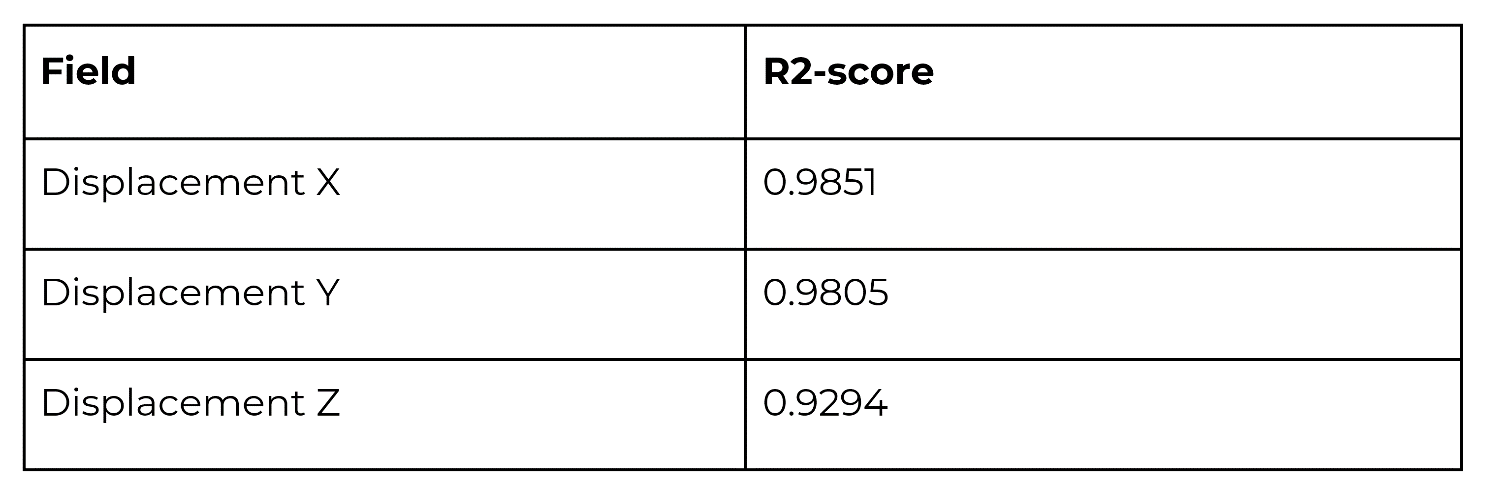
表1:テストセットの変位場に対するサロゲートモデルの精度
「わたしたちは、NCSを使うことによってニューラルネットワークが問題の物理を学習することができることを学びました。各ノードの変形応答は、最小距離の応答よりもはるかに滑らかになる傾向があり、結果の品質は劇的に向上します。私たちのレガシー・ソリューションは、R²が85%、誤差が30%でした。この結果は、さらなるアプリケーションの可能性を広げるものです。」
NCSは、最適化ループの中で3次元場の応答予測を利用するだけでなく、追加にソルバーを使うことなくモデルの予測を視覚化できる小さなウェブアプリを作成しました。図2は、FEAシミュレーションと比較したNCSの予測結果をテスト形状で示したものです:
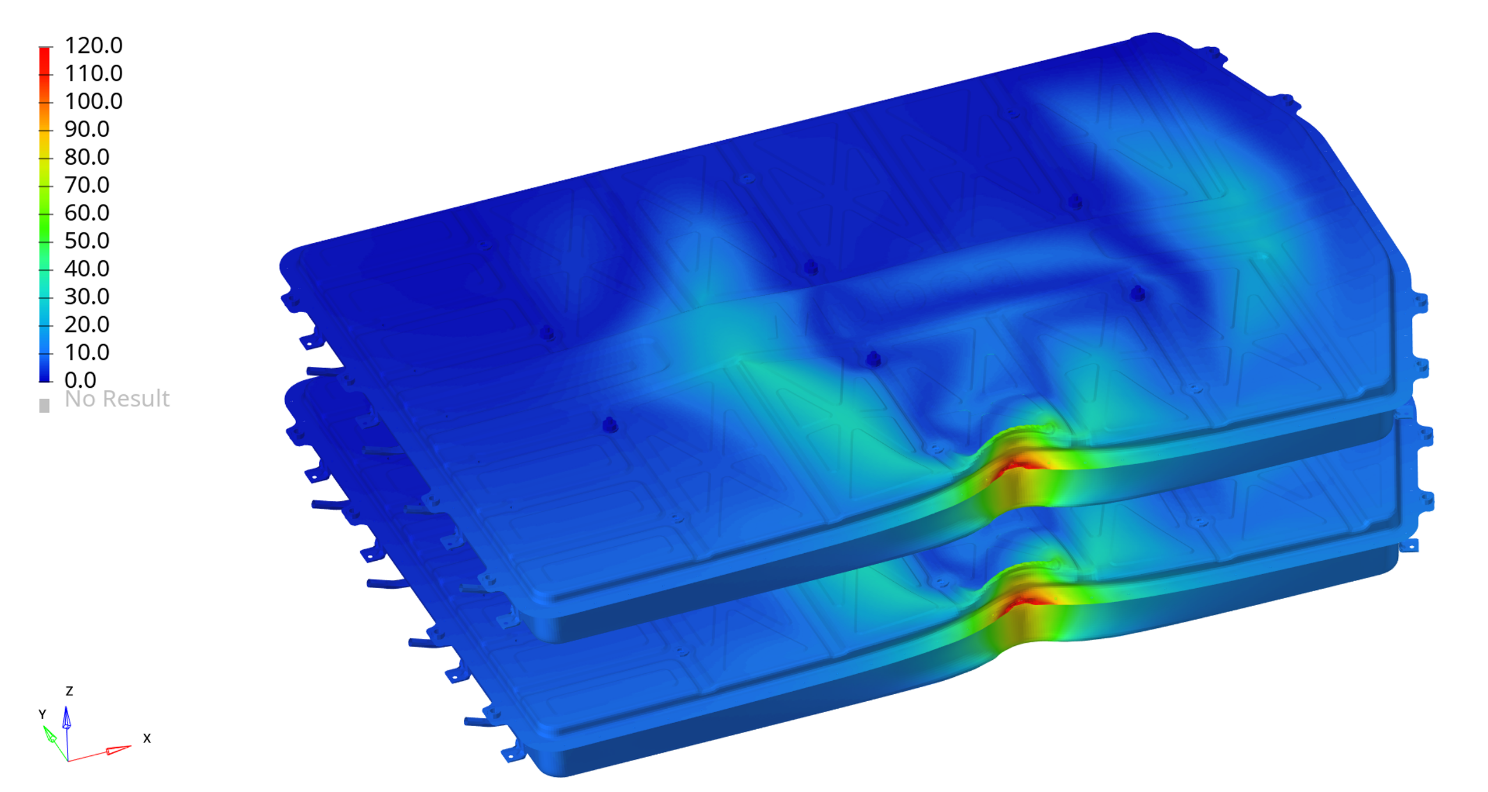
図2:試験形状におけるFEAシミュレーション(上)とNCSによる変位量の予測(下)の比較。予測は複数の時間ステップで実施
「このようなウェブアプリを使えば、本格的なFEA解析をしなくても、設計者が設計に対する直接的なフィードバックを得ることができます。良く定義されたロバストな変形挙動を達成するためには、設計者の経験が重要な意味を持つことがよくありますが、ここで最も重要なのは、エンジニアを間違った方向に導かないようにモデルの品質を理解することです。」
プロセスの核となる信頼性
NCSの信頼性の概念を補強するものとして、エンジニアは、NCSの予測を信頼するかどうかを判断するために、予測ごとに与えられる信頼度指標を使用することができます。図3は、ユーザーがこの指標に基づいて、予測の約10%を信用しない許容閾値を選択した場合、信用される90%の予測に対するR2スコアは、最大荷重に対して0.95になることを示しています。選択した許容閾値を下回る残りの10%の予測については、必要に応じてCAEでシミュレーションすることができます。これらの新しいシミュレーションは、基礎となるAI(深層学習)モデルに、将来、より良い予測を行う方法を教えるために使用できるという利点があります。
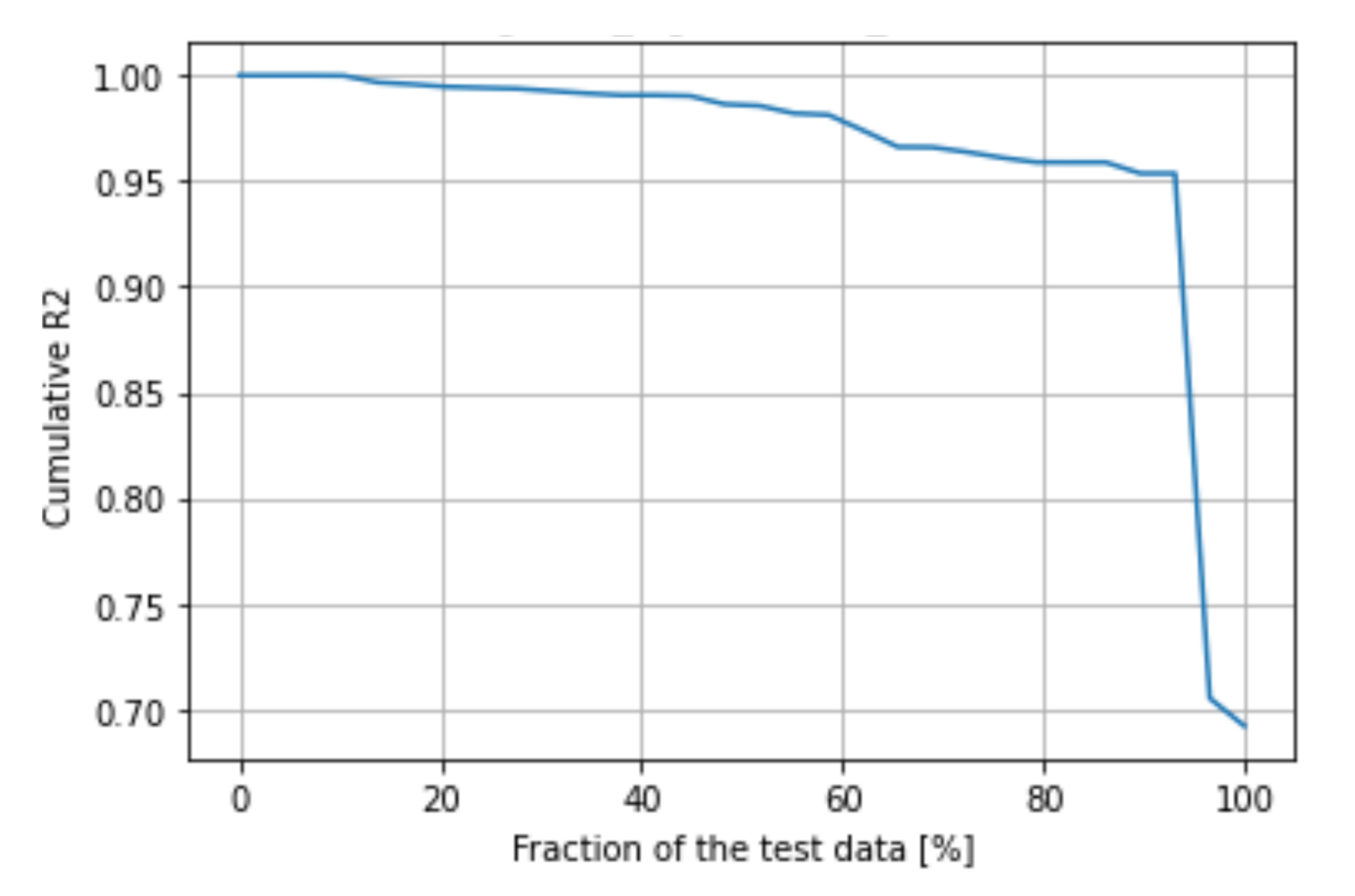
図3:Neural Concept Shapeの不確実性機能を用いると、モデルが与える不確実性指標によって、テストサンプルを低いものから高いものへとソートすることができます。そして、ソートされたサンプルに基づく累積R2を表示します。
この方法は、明確に定義されたパラメータに基づいてバッチで生成された一連のシミュレーションに適用されました。NCSでは、任意の過去の設計を利用してネットワークを学習させることも可能であるため、過去のプロジェクトで得た知識を活用することで、最適な設計をより早く実現することができます。
「この特別な機能を評価したわけではありませんが、将来的な応用に大きな関心があります。SDMシステムに適切に保存され、分類された多くのデータがあれば、この技術を応用して、既知の製品の最適設計をより早く達成することができるでしょう。」
結論:設計者のためのシミュレーション
衝突シミュレーションのスキルを持たない設計者でも、1秒程度で変位や最大荷重を求めることができるこのプロセスは、設計の構想からCAEによる検証まで通常数時間かかることを考えると、革命的と言えるでしょう。
この革新的なアプローチにより、シミュレーション駆動設計の目的は達成されました。将来的には、アルゴリズム駆動設計(最適化アルゴリズムによる設計変更)のような、より有望な進化が待っています。
本記事は、Neural Concept社の下記ウェブサイトに公開されている記事「AMubea using Neural Concept Shape for the Design of Innovative Lightweight Components 」を日本語訳したものです。
Neural Conceptについて
Neural Conceptは、エンジニアリングを強化するためのAIディープラーニングアルゴリズムを開発しています。研究開発サイクルの高速化、製品性能の増強、次世代におけるエンジニアリング課題の解決により、これまでに80社以上の顧客の製品設計方法を革新してきました。同社は2018年、スイスのEPFLにある一流のAI研究室で設立されました。私たちは30人以上のメンバーで構成され、インテリジェンスで産業エンジニアリングの未来を変革するというビジョンに向かい全力を尽くしています。詳しくはこちら
- ※掲載されている製品、会社名、サービス名、ロゴマークなどはすべて各社の商標または登録商標です。